MAIN MACHINE INSTALLATION
Installation
INSTALLATION FLOW CHART
You need the optional paper tray unit or the tandem LCT if you want to install the finisher D686, D687, D688 or D689) or side LCT (D696).
The punch unit is for 1000-sheet booklet finisher (D686), 1000-sheet finisher (D687), 2000-sheet booklet finisher (D688) and 3000-sheet finisher (D689).ACCESSORY CHECK
DescriptionQ’ty D146/D147 D148/ D149/ D150 Power Supply Cord (NA) 1 1 Operation Instructions 4 4 CD-ROM - Driver (NA) 1 - CD-ROM - Driver - 1 CD-ROM - OI 1 1 Sheet - 20 Languages (CHN) 1 1 Seal - 20 Languages 1 1 Holder 1 1 PCU Cover 4 4 Image Transfer Cover 1 1 Sheet - Application : Multi Language :Blank 1 1 Sheet - Application : Multi Language (NA) 1 1 Decal - Paper Tray 1 1 Decal - Original Table 1 1 Decal - Caution : Original : Multi Language 1 1 Plate – Logo 1 1 End Fence 1 1 INSTALLATION PROCEDURE
- Remove the tape from the development units before you turn the main switch on. The development units can be severely damaged if you do not remove the tape.
Installation
Put the machine on the paper tray unit or the LCT first if you install an optional paper tray unit or the optional LCT at the same time. Then install the machine and other options.
- Keep the shipping retainers after you install the machine. You may need them in the future if you transport the machine to another location.
Removal of packing materials and shipping retainers / Removal of PCDU seal
- Remove the machine from the box, and check the items in the package.
- Before lifting up the machine, as there are hidden handles, remove the retainers [A] at the lower front right.
- When you lift the machine, hold the correct parts, as shown in the diagram below.
- Do not lift by holding the scanner unit, etc., because this might deform the machine or break the exterior covers
- Before lifting up the machine, as there are hidden handles, remove the retainers [A] at the lower front right.
- Remove the orange tape and retainers on the outside.
For a machine with preinstalled SPDF, remove the orange tape and retainers on the SPDF.
Make sure to remove the cardboard stabilizer shown below. If you do not, JAM 27 or JAM 64 may occur when printing out onto B4, DLT, or SRA3 sized paper in duplex mode.
Installation
- Remove the paper size decal [A] on the exposure glass.
- Pull out the 1st paper feed tray, and remove the orange tape and retainers.
- Pull out the 2nd paper feed tray, and remove the orange tape and retainers.
- Remove the scanner support [A].
- Open the front cover, and store the scanner support in the storage location [A].
- The factory setting sheet is kept in the position [A].
- Remove the PCDU [A].
Installation
- After removing the orange tape [A], remove the orange tape and red tag [C].
[*]Remove the orange tapes [A].
- When removing the orange tapes, remove the orange tapes one by one without removing the preset seal as shown below.
[*]Return the PCDU to its original position, and connect the harnesses (4 for each unit).
- When you return the PCDU to its original position, check the color (engraving), and set each color unit in the right position.
Installation
- Be careful not to trap the harness with the PCDU front cover. Place the excess portion of the harness on the inside of the inner cover. Also, hook the harness in two places [A].
[*]Attach the ITB unit front cover [A] with the screw provided (3×8) .
[*]Close the front cover.
- When removing the orange tapes, remove the orange tapes one by one without removing the preset seal as shown below.
For machines with preinstalled SPDF: Removal of protective sheet
- Open the SPDF.
- Release the lever [A], open the pressure plate sheet , and pull out the protective sheet [C] slowly.
At this time, remove the filament tape [D].
[*]Close the pressure plate sheet.
[*]Close the SPDF.
- If the protective sheet remains in the SPDF, a paper jam will be detected.
Toner bottle installation
- Open the front cover.
- Shake the toner bottle (Bk) 5 to 6 times.
- Remove the toner bottle protection cap [A].
Installation
- Push the toner bottle into the machine slowly.
- Set the toner bottles (Y, M, C) in the same way.
- Close the front cover.
- When the power is turned on, it will fill up for the first time in about 5 minutes.
1. Attach the part [A] to the paper output tray.
First, insert and attach the front pin (inside the blue circle).
Attaching the decals
- Attach the correct paper tray number and size decals to the paper trays.
- Paper tray number and size decals are also used for the optional paper tray or the optional LCT. Keep these decals for use with these optional units.
Connecting the power cord
- Do not use any connectors other than the power cord provided. Also, do not use an extension cord.
1. Connect the power cord to the machine.
Installation
- Remove the machine from the box, and check the items in the package.
[*]IMAGE QUALITY TEST / SETTINGS
- Remove the tape from the development units before you turn the main switch on. The development units can be severely damaged if you do not remove the tape.
Image quality test
When there are other options to be installed, install according to the procedure for each.- After checking that clamps, etc., have been removed, connect the power plug to the wall socket.
- Turn the main power supply switch ON.
- Check that the operation panel shows the following display. "Please supply the tray with paper."
- The paper size is basically detected automatically.
- Pull out the paper feed tray slowly until it stops.
- While pressing the release lever, adjust the side fence to the paper size to be set.
- Set the back fence.
Checking the copy image with the test chart
Check the copy image with the test chart.Paper setting
1. Set some paper in the feed tray.- SP5-181-001 to 017 (Size Adjust)
1. If necessary, adjust the registration for the paper feed tray. - SP1-002-002 (Side-to-Side Registration Paper Tray 1)
- SP1-002-003 (Side-to-Side Registration Paper Tray 2)
Security Function Installation
The machine contains the Security functions (Data Overwrite Security and HDD Encryption unit) built into the controller board.
If you are installing a new machine, it is recommended to activate the Data Overwrite Security and HDD Encryption unit by selecting "Format All Data" from “System Settings” on the operation panel.
- This method is recommended because there is no user data on the hard drive yet (Address Book data, image data, etc.).
If the customer wishes to activate the Data Overwrite Security and HDD Encryption unit on a machine that is already running, it is recommended to activate the unit by selecting "All Data" from “System Settings” on the operation panel.
- Selecting "All Data" will preserve the data that has already been saved to the hard drive. (If "Format All Data" is selected, all user data saved to the hard drive up to that point will be erased).
Immediately after encryption is enabled, the encryption setting process will take several minutes to complete before you can begin using the machine.
- If encryption is enabled after data has been stored on the disk, or of the encryption key is changed, this process can take up to three and a half hours or more.
The machine cannot be operated while data is being encrypted. Once the encryption process begins, it cannot be stopped.
Make sure that the machine's main power is not turned off while the encryption process is in progress.
If the machine's main power is turned off while the encryption process is in progress, the hard disk will be damaged and all data on it will be unusable.
Print the encryption key and keep the encryption key (which is printed as a paper sheet).
Keep the encryption key in a safe place. If the encryption key is lost and is needed, the controller board, hard disk and NVRAM must all be replaced at the same time.
- "NVRAM" mentioned in here means the NVRAM on the Controller Board.
- "NVRAM" or EEPROM on the BCU has nothing to do with this.
- This method is recommended because there is no user data on the hard drive yet (Address Book data, image data, etc.).
Data Overwrite Security
Before You Begin the Procedure
- Make sure that the following settings (1) to (3) are not at their factory default values.
- Supervisor login password
- Administrator login name
- Administrator login password
If any of these settings is at a factory default value, tell the customer these settings must be changed before you do the installation procedure.
- Make sure that “Admin. Authentication” is on.
[System Settings] -> [Administrator Tools] -> [Administrator Authentication Management] ->
[Admin. Authentication]
If this setting is off, tell the customer this setting must be on before you do the installation procedure. - Make sure that “Administrator Tools” is enabled (selected).
Installation
[System Settings] -> [Administrator Tools] -> [Administrator Authentication Management] -> [Available Settings]
If this setting is disabled (not selected), tell the customer this setting must be enabled (selected) before you do the installation procedure.
Installation Procedure
- Connect the network cable if it needs to be connected.
- Turn on the main power switch.
- Go into the SP mode and push “EXECUTE” in SP5-878-001.
- Exit the SP mode and turn off the operation switch. Then turn off the main power switch.
- Turn on the machine power.
- Do SP5-990-005 (SP print mode Diagnostic Report).
- Go into the User Tools mode, and select [System Settings]
- Exit the User Tools mode.
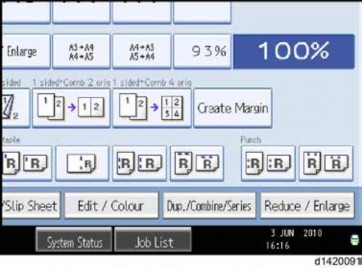
![]() | Icon [1] | This icon is lit when there is temporary data to be overwritten, and blinks during overwriting. |
![]() | Icon [2] | This icon is lit when there is no temporary data to be overwritten. |