Timing | Solutions | Side effect |
![]() | Set SP1-135-001 (Inrush Control) to "1 (ON)". Set SP1-135-002 (Flicker Control) to "1 (ON)". |
|
If it has not been improved in the above, do the following procedures in addition;
(Switch:Rotation Start/Stop:Time:After Reload) to "0 sec". |
| |
![]() | Set SP1-135-002 (Flicker Control) to "1 (ON)". |
|
Troubleshooting
Related SP to Fusing Offsets
SP Name | SP No. | Value |
Print Target Temp. | SP1-105-001 | As initial values + 10 °C are the upper limits, change values to improve offsets. |
Print Target Temp. | SP1-105-003 | |
Print Target Temp. | SP1-105-005 |
SP Name | SP No. | Value |
Print Target Temp. | SP1-105-007 | |
Print Target Temp.: Thin:FC:Center | SP1-105-009 | |
Print Target Temp.: Thin:BW:Center | SP1-105-011 | |
Print Target Temp.: M-thick:FC:Center | SP1-105-013 | |
Print Target Temp.: M-thick:BW:Center | SP1-105-015 |
Troubleshooting
DETAILED DESCRIPTIONS
RE V IS ION H IST ORY | ||
Page | Date | Added/ Updated/ New |
None |
Detailed Descriptions
DETAILED DESCRIPTIONS
GUIDANCE FOR THOSE WHO ARE FAMILIAR WITH PREDECESSOR PRODUCTS
CHANGES FROM THE PREVIOUS MACHINE
Scanner
ItemsMP C2003/C2503
/C2011MP C6004/C5504/C4504
/C3504/C3004
MP C2004/C2504
Scanner type
-Short focus scanner
For distortion correction: After replacing the scanner carriage, the correction value specified on the supplied sheet in the SP code must be entered. For details, see page 4-37 "Scanner Carriage".Scanner carriage storage upon shipping
NoneThe scanner carriage must be moved to the lock position to lock the carriage to the scanner frame before shipping. Main scanning magnification adjustment
Not availableMagnification adjustment is available for the main scanning direction with SP4-871-003,
-004.
ItemsMP C2003/C2503
/C2011MP C6004/C5504/C4504
/C3504/C3004
MP C2004/C2504
SIO
AvailableNot available
The functions of this old board are built into the IPU.Copy data security function
Available by option
Available by default on the IPU
Process Control
ItemsMP C2003/C2503
/C2011MP C6004/C5504/C4504
/C3504/C3004
MP C2004/C2504
MUSIC
Executing rough adjustment -> fine adjustment onlyProcess upon execution of SP2-111-004 (Forced Line Position Adj.: mode d) and [Color Registration] in the User Tools have been changed. - Normal Operation: rough adjustment -> fine adjustment -> contact MUSIC (new process)
- With Imageable Area Extension Unit: rough adjustment -> fine adjustment
Laser Exposure
ItemsMP C2003/C2503
/C2011MP C6004/C5504/C4504
/C3504/C3004
MP C2004/C2504
Laser unit
LD 1 beamMPC4504/C5504/C6004:
LD 4 beams
MP C3004/C3504:
LD 1 beam
LD 1 beam
PCDU (Photo Conductor and Development Unit)
ItemsMP C2003/C2503
/C2011MP C6004/C5504/C4504
/C3504/C3004
MP C2004/C2504MPC4504/C5504/C6004: The seals for all colors
Removal of PCDU seal
The seals must be pulled out for all colors.must be wound up.
MP C3004/C3504:
The seal for K must be wound up with a special
The seals must be pulled out for all colors.tool, and the seals for CMY must be pulled out
PCU
DC charge roller (Contact type) Correction SP value must be input when PCU is replaced
No lubricant bar Discharge lamp is in the main frame
AC charge roller (No contact type) Lubricant bar
No discharge lampDC charge roller (Contact type) Correction SP value must be input when PCU is replaced
No lubricant bar Discharge lamp is in the main frame
ItemsMP C2003/C2503
/C2011MP C6004/C5504/C4504
/C3504/C3004
MP C2004/C2504MPC4504/C5504/C6004: OD (One-way circulation of developer) system
Development unit
Two mixing coils, two-way circulationMP C3004/C3504:
K: OD (One-way circulation of developer)Two mixing coils,
two-way circulationsystem CMY: Two mixing coils, one way circulation
Waste Toner
ItemsMP C2003/C2503
/C2011MP C6004/C5504/C4504
/C3504/C3004
MP C2004/C2504Waste toner cover
With latch
Without latch
Image Transfer and Paper Transfer
ItemsMP C2003/C2503
/C2011MP C6004/C5504/C4504
/C3504/C3004
MP C2004/C2504TM/ID sensor shutter
Available
Not Available
Detailed Descriptions
Feed / Transport Part
ItemsMP C2003/C2503
/C2011MP C6004/C5504/C4504
/C3504/C3004
MP C2004/C2504
Bypass tray / Main machine jam code
-The following codes are used to isolate the cause:
Main tray paper exit
-Tray draw-in mechanism
Not Available
Available
Not AvailablePaper feed sensor/ Paper exit full sensor
Not Available
Available
Not AvailablePaper thickness (Duplex)
52 - 169 g/m2
52 - 256 g/m2
52 - 169 g/m2
Removing wrinkle in trayScrewed with
L-shaped sheet metalSupport component and decal are provided User installable - JAM048: Transport Sensor Lag Jam from Bypass Tray
- JAM051: Transport Sensor Lag Jam from 1st Feed Tray
- Improved stacking performance after feedout by adding resilience to the paper with the paper exit driven roller (drum shape).
- To prevent paper jam when the paper is delivered from the machine’s paper exit to the internal exit peripherals, attach the paper support guide (supplied with the peripherals).
- Replaced the paper exit driven roller to a flat type roller to prevent jamming when paper is fed to the internal exit peripherals.
- Fusing
ItemsMP C2003/C2503
/C2011MP C6004/C5504/C4504
/C3504/C3004
MP C2004/C2504
Curl correction
Not AvailableEquipped with a curl correction mechanism at the fusing exit.
Fusing shield plate
AvailableMP C6004/C5504/C4504:
Available
MP C3004/C3504:
Not Available
Not Available
Fusing shield plate position sensor
2MP C6004/C5504/C4504:
1
MP C3004/C3504:
-
-Heat conduction plate
Not Available
AvailableOthers - Changed the drawer connector location - Changed the drawer connector location:
[A]: MP C6004/C5504/C4504/C3504/C2504/C2004 : MP C2003/C2503/C2011
Detailed Descriptions
Electrical Parts
ItemsMP C2003/C2503
/C2011MP C6004/C5504/C4504
/C3504/C3004
MP C2004/C2504
SIO
AvailableNot available
The functions for this old board are included on the IPUHuman detection (Proximity sensor)
Not AvailableAvailable
Equipped with the proximity sensor (human detection sensor).
OPU1st generation Smart Operation Panel
2nd generation Smart Operation Panel
Exterior Cover / Air Flows (Fan Control)
ItemsMP C2003/C2503
/C2011MP C6004/C5504/C4504
/C3504/C3004
MP C2004/C2504
Air flow
8 fansMP C6004/C5504/C4504:
10 fans
MP C3004/C3504:
7 fans
7 fans
Duct
-Increased the rigidity of the duct Changed the duct shape
Noise control
-- Equipped with a Helmholtz silencer
- Labyrinth structure of the exterior
- Labyrinth structure of the exterior:
- Exterior parts engage with each other to reduce the leaking of the driving noise.
Drive Parts
ItemsMP C2003/C2503
/C2011MP C6004/C5504/C4504
/C3504/C3004
MP C2004/C2504
Noise control
-From the usual non-helical gears [A], we increased the use of helical gears to increase the efficiency of engagement. This has also reduced the rattling noise due to the increased gear engagement.
[TD][/TD]
[TR]
[TD]
Silencing grease for the drive parts[/TD]
[TD]
-[/TD]
[TD]Grease is applied to over 100 parts, including gears, shafts, and bearings, to reduce the driving noise.[/TD]
[TD][/TD]
[/TR]
Detailed Descriptions
Others
Changing the Default Value for the Binding Margin
Until the last model, the default value for the binding margin was “5 mm on the right (on the back of the sheet)” when copying on both sides, in order to align the prints on both sides when punching. This has occasionally caused the paper edges to appear on the printed copies.
Thus, in this series, the default value for the binding margin is changed to “0 mm on the right (on the back of the sheet)” and the default value to mask the paper edge (SP mode) is also changed to reduce the chance of the black streak appearing.
Binding Margin Setting
Changed Default Values in the SP mode
SP4-012-001 (Set Scale Mask Book:Sub Ledge) 0 -> 1mm SP4-012-003 (Set Scale Mask Book:Main:Ledge) 0 -> 1mm
SP6-006-007 (ADF Adjustment Rear Edge Erase Front) 0 -> -2.3mm
SP6-006-014 (ADF Adjustment T-Edge Erase (1-Pass): Front) -1.5 -> -3.0mm SP6-006-015 (ADF Adjustment T-Edge Erase (1-Pass): Front) -1.5 -> -2.5mm
[*]COMPONENT LAYOUT
SCANNER UNIT
No. Description No. Description 1 Operation panel 6 Auto paper size (APS) sensor
2Anti-condensation heater (Scanner heater) *1
7
Scanner lamp unit (LED)3 Scanner HP sensor 8 Scanner motor 4 ARDF/Platen cover sensor 9 Sensor board unit (SBU) 5 Auto paper size (APS) sensor
* Service part
Detailed Descriptions
LASER EXPOSURE UNIT
No. Description No. Description 1 Laser optics positioning motor (Y) 5 Polygon mirror motor 2 Synchronizing detector board: M/Y-S 6 LD drive board (M/Y) 3 Laser optics positioning motor (M) 7 LD drive board (Bk/C)
4Laser optics positioning motor (C)
8Synchronizing detector board: Bk/C-S IMAGE TRANSFER UNIT
No. Description 1 Temperature and humidity sensor 2 Interlock switch: right door 3 ITB contact and release sensor 4 Paper transfer contact and release motor 5 TM/ID sensor (rear) 6 TM/ID sensor (center) 7 TM/ID sensor (front)
Detailed Descriptions
PCDU
No. Description No. Description 1 PCDU (Y) 3 PCDU (C) 2 PCDU (M) 4 PCDU (Bk) TONER SUPPLY / WASTE TONER BOTTLE
No. Description No. Description 1 ID chip contact board (Y) 10 Toner end sensor (Y) 2 Toner bottle drive motor (Y) 11 Toner supply motor (M) 3 ID chip contact board (M) 12 Toner end sensor (M) 4 Toner bottle drive motor (M) 13 Toner supply motor (C) 5 ID chip contact board (C) 14 Toner end sensor (C) 6 Toner bottle drive motor (C) 15 Toner end sensor (Bk) 7 ID chip contact board (Bk) 16 Toner supply motor (Bk) 8 Toner bottle drive motor (Bk) 17 Waste toner bottle full sensor 9 Toner supply motor (Y) 18 Waste toner bottle set sensor
Detailed Descriptions
PAPER FEED UNIT
No. Description No. Description 1 Tray set switch (1st feed tray) 8 Transport sensor (2nd Feed Tray) 2 Lift motor (1st feed tray) 9 Paper end sensor (2nd feed tray) 3 Tray set switch (2nd feed tray) 10 Upper limit sensor (2nd feed tray) 4 Lift motor (2nd feed tray) 11 Transport sensor (1st feed tray) 5 Registration sensor 12 Paper end sensor (1st feed tray) 6 Paper size switch (2nd Feed Tray) 13 Upper limit sensor (1st feed tray) 7 Anti-condensation heater DUPLEX UNIT
No. Description No. Description 1 Duplex entrance motor 5 Bypass pick-up solenoid 2 Right door open/close sensor 6 Bypass / Duplex motor 3 Duplex entrance sensor 7 Duplex exit sensor
4Duplex guide plate open/close sensor
8
Bypass paper end sensor
Detailed Descriptions
BYPASS UNIT
No. Description 1 Bypass width sensor 2 Bypass length sensor FUSING UNIT
No. Description No. Description 1 Pressure roller HP sensor 7 Fusing sleeve thermostat (center) 2 Thermopile (edge) 8 Non-contact thermistor (center) 3 Thermopile (center) 9 Pressure roller thermistor (center) 4 Fusing exit sensor 10 Non-contact thermistor (edge)
5
Fusing lamp
11Pressure roller thermistors (edge, full-bleed edge) 6 Fusing sleeve thermostat (edge)
Detailed Descriptions
PAPER TRANSFER / PAPER EXIT
No. Description No. Description 1 Reverse motor 5 Fusing entrance sensor 2 Reverse sensor 6 Fusing exit sensor
3
Paper exit sensor
7Fusing exit drive solenoid (installed on the main machine) 4 PTR open/close sensor 8 Paper exit solenoid AIR FLOW
No. Description No. Description
1
Paper exit cooling fan
5Imaging temperature sensor (Thermistor) 2 Development intake fan 6 Toner supply cooling fan 3 PSU cooling fan 7 Fusing exhaust fan 4 Ozone exhaust fan
Detailed Descriptions
DRIVE UNIT
No. Description No. Description 1 Imaging IOB 6 Transport motor 2 Development motor: CMY 7 PCU motor: Black / ITB drive motor 3 PCU motor: CMY 8 Registration motor 4 Development Solenoid 9 Fusing motor 5 Paper feed motor 10 Paper exit / Pressure release motor BOARD / SWITCH
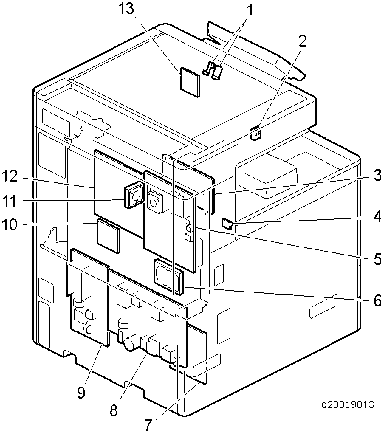
No. | Description | No. | Description |
1 | Proximity sensor (Human detection sensor) | 8 | PSU (DC power) |
2 | Interlock switch: front cover | 9 | PSU (AC controller board) |
3 | HVP_TTS | 10 | BCU |
4 | Main power switch | 11 | Controller box cooling fan |
5 | Control board | 12 | IPU |
6 | HDD | 13 | Proximity sensor (Human detection sensor) board |
7 | Paper transport IOB |
Detailed Descriptions
SCANNING
OVERVIEW
The short focus scanner is realized by implementing a lens block (SBU, CCD, and Lens) on the carriage.
After the scanner lamp unit emits the light to the document, the light goes through route shown below and reaches the CCD.
Scanner lamp unit (LED) -> Original -> 1st mirror (13) -> 2nd mirror (3) -> 3rd mirror (6) -> 2nd mirror (3) -> 4th mirror (5) -> 5th mirror (14) -> lens -> pre-sensor lens -> CCD
No. Description No. Description 1 Sheet-through exposure glass 9 Sensor board unit (SBU) 2 Exposure glass 10 CCD 3 2nd mirror 11 Pre-sensor lens 4 Scanner lamp unit (LED) 12 Lens 5 4th mirror 13 1st mirror 6 3rd mirror 14 5th mirror
7
Scanner motor
15Anti-condensation heater* (Scanner heater) 8 APS sensors
*Service part
Reading System
Two scan modes are available: book mode (platen mode) and ADF mode (sheet-through method).
In book mode (platen mode), the scanner scans the document from left to right.
When the ADF is used (ADF mode), the scanner is fixed in the home position on the left side, and the document is transported and read (sheet-through method).
Scanner
Scanner lamp
The light source is an LED. The LED emits little heat (low power consumption), and has excellent light output rise characteristics.
CCD
The 3 line color CCD converts shade in the document to 3 color (B, G, and R) electrical signals. The use of a 4.7 µm image CCD achieves low-cost and compactness.
Reflection plate (reflector)
The reflection plate reflects light from the scanner lamp, and collects light for the document read unit. The light which illuminates the document is adjusted to be the same on the left and right so as not to cast any shadow on the document.
White reference seal
A white reference seal for shading correction is affixed to the underside of the scale on the left of the MFP. This is read by the scanner and CCD when the power is ON. The data read are temporarily stored in a RAM, and used for correction of document image data.
Detailed Descriptions
MECHANISM
Scanner Drive
The scanner is driven by the scanner motor [D] via the timing belt [C]. For each mode, reading is completed in one pass.
Position control of the scanner carriage is based on the scanner HP sensor [A].
Operation Flowchart
Overall Flowchart
Scanner Carriage Storage Control
To protect the scanner carriage, the carriage must be locked to the scanner frame before shipping. The scanner can be moved to the shipping lock position with SP4-806-001 (Scanner carriage storage operation).
If pre-shipping check is required, make sure to move the scanner carriage to the right position with SP4-806-001 and mount the locking parts.
SC121-00 will occur when the power is turned on or scanning takes place while the carriage is locked.
Document Size Detection
Detailed Descriptions
In this MFP, for document size detection, two reflecting sensors are used for the sub scanning direction, and a CCD is used for the main scanning direction.
Sub scanning direction
The document size is detected by ON/OFF of the sensor. The pressure plate open/close sensor is used for document size detection timing. When the pressure plate open/close sensor has changed from "no cover" to "cover," the size is detected.
Main scanning direction
RGB color densities at 3 locations (S1, S2, S3) are detected by a CCD, and when any of the RGB densities is 12 digits or more, it is determined that a document is present.
The pressure plate open/close sensor is used for document size detection timing. When the pressure plate open/close sensor detects "no cover," the scanner lamp is moved to the right; when it detects "cover," the scanner lamp is moved to home position while lit, and during this time, the size is read.
Document size Sensor response
Size
DirectionDimensions (main × sub)
S1
S2
S3
L1
L2A3 SEF 297x420 - -
B4 SEF 257x364 -
-
A4 SEF 210x297
- -
- A4 LEF 297x210 - -
- - B5 SEF 182x257 - - -
- B5 LEF 257x182
- - - Document size Sensor response A5 SEF 148x210 - - - - - A5 LEF 210x148
- - - - B6 SEF 128×182 - - - - - B6 LEF 182×128 - - - - - DLT SEF 11"×17" - -
-
10×15 SEF 10"×15" -
- -
USB4 SEF 10"×14" -
- -
LG SEF 8 1/2"×14"
- - -
Oficio SEF 8 1/2"×13.4"
- - -
Foolscap SEF 8 1/2"×13"
- - -
Folio SEF 8 1/4"×13"
- - -
F SEF 8"×13"
- - -
LT SEF 8 1/2"×11"
- -
- LT LEF 11"×8 1/2" - -
- - 8×10 SEF 8"×10"
- -
- 10×8 LEF 10"×8" -
- - -
Executive
SEF7 1/4"×10
1/2"
-- -
- HLT SEF 5 1/2"×8 1/2" - - - - - HLT LEF 8 1/2"×5 1/2"
- - - - 8kai SEF 267×388 -
- -
16kai SEF 194×267 - - -
- 16kai LEF 267×194 -
- - -
Detailed Descriptions
- The document width (main scanning direction) is detected by the sensor indicated with
How to check the sensor state- SP4-301 (Operation Check APS Sensor)
How to read the screen (7)00000000(0)
0: no document
1: document present
When the sensor responds, bit 0 is displayed as "1." - SP4-310 (Scan Size Detect Value)
Viewed from the control panel, labeling positions from rear to front S1-S3 in that order, the RGB density at each position is displayed in digit units (the value just before scan is displayed).
Other - SP4-303 (Min Size for APS)
Sets the display when non-standard (small size) size original is detected. 0: Display message "Original size unknown".
1: Operate assuming the original size is A5 LEF (HLT LEF for inches). - SP4-305-001(8K/16K Detection)
By changing this SP, you can change between A4 size/letter size or Chinese paper size (8×16).
0: Normal setting. (Default)
1: When detecting A4/LT size -> Assume that it is A4 when SEF, LT when LEF. 2: When detecting A4/LT size -> Assume that it is LT when SEF, A4 when LEF. 3: Change to 8K/16K settings.
A3, B4 -> 8K LEF
A4 LEF, B4 LEF, A5 LEF -> 16K LEF A4 SEF, B4 SEF, A5 SEF -> 16K SEF - SP5-126 (Set F-size Document)
Selects the paper size for the F-size original.
0: When detecting Foolscap -> Assume that the size is 8 1/2"x13". (Default) 1: When detecting Folio -> Assume that the size is 8 1/4"x13".
2: When detecting F -> Assume that the size is 8"/13". - SP4-308 (Scan Size Detection)
Sets CCD original size detection and APS original size detection. 0: Disable: Not detect original size
1: Enable: Detect original size by the CCD unit
2: APS: APS sensor is used for detecting original size. - SP4-309-004 (Scan Size Detect:Setting LED PWM Duty)
If the user specifies that the pre-scan lamp is too bright, the brightness pre-scan can be reduced by decreasing the value of SP4-309-004 (Scan Size Detect:Setting LED PWM Duty). However, if the lamp brightness is reduced, size detection for a document with a large number of solid images will be less accurate. - SP5-135 (LG_Oficio Change)
- 1: When detecting LG size -> Assume that the size is 8 1/2"x14".
Improved Tolerance to Black Lines When Paper Passes through ARDF/SPDF
The original document does not come in contact with the sheet-through exposure glass, which prevents adhesive dirt (ball pen ink) on the document from adhering to the sheet-through exposure glass.
ADF cross-section diagram, non-contact scanning
[A]: Sheet
: Sheet-through exposure glass [C]: Read position
[D]: Document
- Contact scanning
As the document comes in contact with the sheet-through exposure glass this is useful for dealing with adhesion of free dirt particles (paper scraps, etc.). (Self-cleaning mechanism using paper)
On the other hand, sticky dirt adhering to the document sticks to the sheet-through exposure glass, and may give rise to the appearance of black lines.
ADF cross-section diagram, contact scanning
Detailed Descriptions
[A]: Sheet-through exposure glass : Read position
[C]: Document
If black lines due to free dirt particles appear within a short time, such as when users have documents with large amounts of paper scraps, you can change from the non-contact scanning system to the contact scanning system with the procedure in Troubleshooting - Vertical Streaks on Copies due to Scanning Problems.
[*]Reference (reading position correction)
By changing SP4-020-001 (Dust Check Dust Detect:On/Off), when dirt is detected at the reading position, the reading position may be changed to avoid the dirt.
(If it cannot be avoided, an alert is displayed on the control panel advising the user to perform target glass cleaning).
Image diagram
[A]: Read position
: Sheet-through exposure glass [C]: Dirt
- Dirt is detected when a document passes through, so the alert will not disappear until reading of the next document begins, even after the sheet-through exposure glass cleaning is performed.
- If dirt is detected not on the sheet-through exposure glass but on the background guide plate, the alert will not disappear even if the glass is wiped.
- The time required for the first copy is slightly (almost imperceptibly) longer.
- The detection threshold value can be changed using SP4-020-002 (Dust Check Dust Detect:Lvl). (The larger the value is, the smaller the dirt particles that can be detected become.)
- It is prohibited to change the setting of SP4-020-003 (Dust Check Lvl Dust Reject:Lvl).
Difference between Non-contact Transport and Contact Transport in DF Scanning
Transport Method
Non-contact Transport
Contact Transport
Descriptions
Because of the film attached to the glass, the original doesn’t contact the glass.
While passing, the original contacts the glass.
Merit
It almost never causes stripes on the image that arise from foreign substances transferring from the original to the glass.It almost never causes stripes on the image that arise from dust on the glass, because the glass is cleaned by contact with the transported original.
Demerit
Compared with the contact method, stripes on the image caused by dust occur more often.Compared with the non-contact method, stripes on the image caused by foreign substances transferred from the surface of an original to the glass occur more often. Transport Method
Non-contact Transport
Contact Transport
Aim
To improve prevention of stripes in the image caused by sticky foreign substances.Considering the target users of this machine, it’s important to improve prevention of stripes caused by dust in the path
Notesheet-through glass with the film attached on the glass.
non-contact, or vice versa) by replacing some parts.*1
-- Be sure to replace the
- When you attach the film on the glass, you need to keep the left scale attached on the glass in order to fix the location of the film.*1
- You can change the method (contact method to
Detailed Descriptions
*1: For details, page 6-309 "Vertical Streaks on Copies due to Scanning Problems".
Anti-Condensation Heater
A
Under low temperature conditions, condensation may appear on optical parts (such as mirrors). This will cause image deletion, blacked out images, and gray images. As a countermeasure, there is an anti-condensation heater [A] that is an optional service part. This heater turns on automatically when the power source turns off.
Anti-condensation heater
Detailed Descriptions
- SP4-301 (Operation Check APS Sensor)
- The document width (main scanning direction) is detected by the sensor indicated with
[*]IMAGE PROCESSING
MECHANISM
SBU
Functions
Performs Black level correction and White level correction, Creating the SBU test pattern, and A/D conversion.
This machine is equipped with a short focus scanner and the SBU is located on the scanner carriage.
Operation overview
Samples 2 analog signals (ODD, EVEN) from RGB output from the 3-line CCD, and converts them to digital signals by an A/D converter. The digital signals are output to the IPU.
SP correction value storage
The SBU correction value is stored in an EEPROM on the BCU.
Execute the following SP settings when the scanner carriage is replaced. (Lens block is located on the scanner carriage.)- SP4-871-002 (Distortion Correction Distortion Initialization)
- SP4-880-001 (Dot shift amount between R Line and G Line).
- SP4-880-002 (Dot shift amount between G Line and B Line).
SBU Test Mode
There is an SP code to create a test pattern which can be used as a diagnostic tool to troubleshoot problems in the SBU: - SP4-699-001 (SBU Test Pattern Change) Pattern 1: fixed value
Pattern 2: main scanning gradation pattern Pattern 3: width scanning gradation pattern
Pattern 4: main scanning/width scanning lattice pattern SBU has a function to generate four test patterns.
IPU
Image processing function overview
The image signals from the SBU are subjected to various image processing, and output to the controller (memory). The image signals from the controller (memory) are received, and output to the LDB (the LDB is provided in the write unit).
Image processing overview (copy application)
Digital signal data output from the SBU is subjected to shading correction and line interval correction, as well as image processing, which are performed by the IPU. Finally, the data is sent to the machine as digital signals-4 bit/pixels.
Image processing items
Details
Shading correctionCorrects for uneven scanner lamp lighting, and scatter in CCD light receiving sensitivity.
Line interval correctionLine shift during subscanning magnification/reduction by scanner. Corrects integer part.
Dot correctionLine shift during subscanning magnification/reduction by scanner. Corrects below decimal point. Vertical line correction Corrects a vertical striped image during sheet-through ADF. Image area separation Determines text parts and photo parts of image. Scanner gamma correction Corrects scatter of image data relative to exposure amount. From reflectivity linear to density linear. Filter Performs image sharpness adjustment and removes moire. ADS Performs natural complexion removal in full color mode. Color compensation preprocessing
Determines hue in masking mode, and improves chromaticity.
Color compensationConverts RGB data to density value CMYK data of color materials.
Image magnification changeArbitrarily changes main scanning magnification, subscanning fixed image reduction and magnification of scanner image. Image processing items
Details
Image shift functionShifts image data in the main scanning or subscanning directions. Image binarization function
In scanner mode, outputs a binary signal.
Image maskMasks an area outside a frame of an arbitrary region in scanner or printer data. Image compression/expansion
Compresses or expands an image.Printer gamma correction Adjusts exposure amount of photosensitive body relative to image density. Gradation processing Applies 600dpi, 4bit 16 value gradation processing.
LASER EXPOSURE
OVERVIEW
Four stations (one for each color).
No. Description No. Description 1 2nd mirror 8 F-theta lens-M/Y 2 Laser optics positioning motor (C) 9 LD drive board 3 Laser optics positioning motor (M) 10 Polygon mirror motor 4 2nd mirror 11 LD drive board 5 Laser optics positioning motor (Y) 12 Cylinder lens 6 Cylinder lens 13 F-theta lens-Bk/C 7 1st mirror 14 2nd mirror
Detailed Descriptions
Parts Construction
The write unit comprises a housing and the following main parts:
No. Description No. Description 1 1st mirror 5 F-theta lens 2 Dust shield glass 6 Soundproof glass 3 PCU (Y,M, C, K) 7 Polygon mirror motor 4 2nd mirror
No. Description No. Description
1
LD drive board (M/Y)
4Synchronizing detector board: Bk/C-S
2
LD drive board (Bk/C)
5Synchronizing detector board: M/Y-S 3 Cylinder lens (Bk/C) 6 Cylinder lens (M/Y)
Detailed Descriptions
MECHANISM
LD Drive Board
The LD Unit is provided with two LD drive board. The beam system is a 1 beam type. The LD drive board comprises an LD (laser diode), PD (photodiode) and LD control unit.- The LD outputs the laser light to the PCU.
- The PD continuously detects laser light from LD, and outputs it to the LD control unit.
- The LD control unit adjusts the light amount of the LD based on the output signal of the PD. LD control board adjustment is not required in the field.
LD Safety Switch
To prevent the laser beam from turning on when the front cover or right door is open, the 5V supply to the LD drive board is interrupted when the interlock switch is open.
Circuit Diagram
Line Scanning Mechanism
[A]: Dust shield glass : 1st mirror
[C]: F-theta lens
[D]: Polygon mirror motor
- Mirror, lens
Laser diodes of each color emit light to match the paper transport timing. After passing through the cylinder lens (laser beam width correction), polygon mirror motor (main scanning line scan), F-theta lens (dot position correction and optical face tangle error correction), it reaches the drums of each color.
The F-theta lens has a two-stage integrated construction, and 2 color beam correction is performed with one lens. - Polygon mirror motor
The polygon mirror motor comprises two (upper and lower) 6-faced mirrors formed in an integral construction (these are combined in one unit).
In this MFP, 4 color simultaneous write is performed by the LD irradiating a polygon mirror.
* The rotation speed of the polygon mirror motor is controlled by LD/ Polygon mirror motor. - Synchronization sensor
There are two synchronization sensors, i.e., one on the K-C side, and one on the M-Y side. Each sensor detects light from one color, and synchronization for two colors is calculated from this.
There is only one sensor for each color. The sensor at the leading edge of the main scan line has been removed. - Scan line inclination and automatic adjustment mechanism
- The laser optics positioning motor installed on the 2nd mirror adjusts the scan line inclination. This is done during automatic image position correction.
Detailed Descriptions
- Mirror, lens
[*]PROCESS CONTROL
MECHANISM
Sensor Construction
The ID Sensors (also called the TM/ID sensors) are used to measure the amount of toner on the transfer belt and to correct any errors in color registration.
The TD sensor (also called the
Outline of the ID Sensors
The ID sensors are fixed onto the main frame, against the surface of the transfer belt. Color registration is checked by all three sensors; the front [A], center , and rear [C].
The center sensor acts as an ID sensor and a MUSIC sensor.
Outline of the TD sensor
In this model, a non-contact toner density (TD) sensor, which we also call a mu
The TD sensor is attached on the lower side of the development unit. Unlike a HST sensor, the board of the TD sensor is exposed. So there is a cover around the sensor to protect it and to maintain a good contact between the sensor and development unit.
The TD sensor measures the permeability of the developer without contacting it, from the outside of the case, and converts the measured value to the toner density.
According to the toner density measured by this sensor, the proper amount of toner is supplied to the developer.
A counter corresponding to the frequency is used as the unit of TD sensor output. Thus, unlike a HST sensor which directly detects Vt, the TD sensor output is converted into Vt for toner supply control.
In the TD sensor, there is an ID chip storing the machine identification information, the running distance information of development unit and PCU, and other information used by image density control.
[*]PROCESS CONTROL
Outline
Process control adjusts the condition of the imaging hardware to maintain a constant image density. Process control is executed at the following times.
Process Control | Operative Condition | Related SPs | |
1 | PowerON ProCon :Set | When a certain time has passed after the previous job end (Except when recovering from an SC or jam) | SP3-530-001 SP3-530-002 SP3-530-003 SP3-530-004 SP3-530-005 SP3-530-006 SP3-530-007 SP3-530-008 |
2 | JobEnd ProCon :Set | When the value of the job end counter becomes more than the threshold (At job end) | SP3-534-001 to 004 SP3-534-011 to 014 |
Process Control | Operative Condition | Related SPs | |
3 | Interrupt ProCon :Set | When the value of the job interrupt counter becomes more than the threshold | SP3-533-001 to 004 SP3-533-011 to 014 |
4 | Non-useTime Procon :Set | When the value of the non-use time counter becomes more than the threshold | SP3-531-001 to 004 |
5 | Manual ProCon :Exe | When SP 3-011 is used | SP3-011-001 to 005 |
6 | Toner End Recovery | After the Toner End Status is cleared (Recovery is NOT done in the near end status) | - |
7 | Initial Developer Setting Process Control | When the machine detects a new PCU or development unit | - |
Detailed Descriptions
Result Code for Executing Process Control
Check the following SPs.
- SP3-012-001 to 010 (Front)
- SP3-012-011 to 020 (Center)
- SP3-012-021 to 030 (Rear)
Category | Code | Result name | Description |
00 and larger | 00 | Not executed | Factory default setting (SP default) |
10 and larger Result (Normal) | 11 | Succeeded | - |
40 and larger ID Sensor | 41 | ID sensor output error (Max) | Vt > Max |
42 | ID sensor output error (Min) | Vt < Min |
Category | Code | Result name | Description |
43 | ID Sensor error (Max) | Development gamma is in target, but Vt value is less than upper limit. | |
44 | ID Sensor error (Min) | Development gamma is in target, but Vt value is less than lower limit. | |
45 and larger ID Pattern detection | 45 | ID Pattern extract error | Cannot detect ID Pattern |
50 | Vmin_Bk/K2 error (Max) | K:Vmin_Bk / CMY:K2 > Max | |
51 | Vmin_Bk/K2 error (Min) | K:Vmin_Bk / CMY:K2 < Min | |
52 | K5 error (Max) | K5 > Max | |
53 | K5 error (Min) | K5 < Min | |
54 | K5 calculated approximate point error | K5 calculated approximate point < Min | |
55 | Development gamma error (Max) | Development gamma > Max | |
56 | Development gamma error (Min) | Development gamma < Min | |
57 | Start developing voltage: Vk error(Max) | Start developing voltage: Vk > Max | |
58 | Start developing voltage: Vk error(Min) | Start developing voltage: Vk < Min | |
59 | Not enough valid data | Adhesion amount data for development gamma calculation point is under 2. | |
90 and larger Result(End) | 90 | Potential not adjusted | Potential control method is set as [0:FIX]. |
99 | Stopped | Stopped by door open, power off, error. (Set when execute.) |