Cause verification | Problem Judgement |
Turn the referenced motor OFF with OUTPUT check | Drive sound heard |
Turn the referenced motor ON with OUTPUT check | Drive sound not heard |
Troubleshooting
Solution:
- Reconnect the connector.
- Replace the motor.
- Replace the Paper Transport IOB.
- Replace the harness.
Target Part/SP No.: Transport Motor / SP5-804-028
Cause verification Problem Judgement Turn the referenced motor OFF with OUTPUT check Drive sound heard Turn the referenced motor ON with OUTPUT check Drive sound not heard
Solution:
- Reconnect the connector.
- Replace the motor.
- Replace the Paper Transport IOB.
- Replace the harness.
Target Part/SP No.:Reverse Motor / SP5-804-047 (Inverter Motor:CW:Standard Speed)
Cause verification Problem Judgement Turn the referenced motor OFF with OUTPUT check Drive sound heard Turn the referenced motor ON with OUTPUT check Drive sound not heard
Solution:
- Reconnect the connector.
- Replace the motor.
- Replace the Paper Transport IOB.
- Replace the harness.
Target Part/SP No.:Bypass Length Sensor / SP5-803-024 (By-pass: Sub Scan Length Sensor)
Cause verification Problem Judgement Execute an INPUT check when there is no paper at the position of the referenced sensor. 1: Paper detected Execute an INPUT check when there is paper at the position of the referenced sensor. 0: Paper not detected
Solution:
- Clean the sensor.
- Reconnect the connector.
- Replace the sensor.
- Replace the Paper Transport IOB.
- Replace the harness.
Checking paper jam, or paper status
Check the paper position (Check whether or not the leading edge of the paper, side paper guide, and end paper guide are positioned according to the manual.) Check if the paper has reached the maximum stackable limit of the side paper guide. Reduce the paper to below the stackable limit. Check if extra thin paper or thick paper exceeding the supported paper thickness is being used. Use a supported paper type. Check if the paper thickness and size are detected correctly. Set the paper thickness and size to the correct value. Check if the paper being used produces a lot of paper dust. Change the paper type (if possible). Check if there is no double feeding. Fan the paper. Check if the paper feed tray is not stained with a lot of paper dust. Clean the paper feed tray.
Check if the paper roller is not stained with paper dust.Clean the pick-up roller, feed roller, and friction roller for 1st feed tray. - Check the paper orientation.
- Turn the paper in the feed tray upside down.
Tray 2 Transport Sensor: Lag Jam: Cause Code 052
Target Part/SP No.:Transport Sensor (2nd Feed Tray) / SP5-803-005 (Transport Sensor 2)
Cause verification Problem Judgement Execute an INPUT check when there is no paper at the position of the referenced sensor. 0 aper detected
Execute an INPUT check when there is paper at the position of the referenced sensor. 1: Paper not detected
Solution:
- Clean the sensor.
- Reconnect the connector.
- Replace the sensor.
- Replace the Paper Transport IOB.
- Replace the harness.
Target Part/SP No.: Paper Feed Motor / SP5-804-016 (Feed Motor:CW:Standard Speed)
Cause Verification Problem Judgement Turn the referenced motor OFF with OUTPUT check Drive sound heard Turn the referenced motor ON with OUTPUT check Drive sound not heard
Solution:
- Clean the sensor.
- Reconnect the connector.
- Replace the sensor.
- Replace the Paper Transport IOB.
- Replace the harness.
Target Part/SP No.: Transport Motor / SP5-804-028
Cause verification Problem Judgement Turn the referenced motor OFF with OUTPUT check Drive sound heard Turn the referenced motor ON with OUTPUT check Drive sound not heard
Solution:
- Reconnect the connector.
- Replace the motor.
- Replace the Paper Transport IOB.
- Replace the harness.
Checking paper jam, or paper status
Check the paper position (Check whether or not the leading edge of the paper, side paper guide, and end paper guide are positioned according to the manual.) Check if the paper has reached the maximum stackable limit of the side paper guide. Reduce the paper to below the stackable limit. Check if extra thin paper or thick paper exceeding the supported paper thickness is being used. Use a supported paper type. Check if the paper thickness and size are detected correctly. Set the paper thickness and size to the correct value. Check if the paper being used produces a lot of paper dust. Change the paper type (if possible). Check if there is no double feeding. Fan the paper. Check if the paper feed tray is not stained with a lot of paper dust. Clean the paper feed tray.
Check if the paper roller is not stained with paper dust.Clean the pick-up roller, feed roller, and friction roller for 2nd feed tray. - Check the paper orientation.
- Turn the paper in the feed tray upside down.
Registration Sensor: Lag Jam: Cause Code 057
Target Part/SP No.:Registration Sensor / SP5-803-001
Cause verification Problem Judgement Execute an INPUT check when there is no paper at the position of the referenced sensor. 0 aper detected
Execute an INPUT check when there is paper at the position of the referenced sensor. 1: Paper not detected
Solution:
- Clean the sensor.
- Reconnect the connector.
- Replace the sensor.
- Replace the Paper Transport IOB.
- Replace the harness.
Target Part/SP No.: Bypass/Duplex Motor / SP5-804-071 (Duplex Bypass Motor:CW:Standard Speed)
Cause verification Problem Judgement Turn the referenced motor OFF with OUTPUT check Drive sound heard Turn the referenced motor ON with OUTPUT check Drive sound not heard
Solution:
- Reconnect the connector.
- Replace the motor.
- Replace the Paper Transport IOB.
- Replace the harness.
Target Part/SP No.:Reverse Motor / SP5-804-047 (Inverter Motor:CW:Standard Speed)
Cause verification Problem Judgement Turn the referenced motor OFF with OUTPUT check Drive sound heard Turn the referenced motor ON with OUTPUT check Drive sound not heard
Solution:
- Reconnect the connector.
- Replace the motor.
- Replace the Paper Transport IOB.
- Replace the harness.
Checking paper jam, or paper status
Check if there is no double feeding. Fan the paper.
Paper Exit Sensor: Lag Jam: Cause Code 060
Target Part/SP No.: Paper Exit Sensor / SP5-803-008
Cause verification Problem Judgement Execute an INPUT check when there is no paper at the position of the referenced sensor. 0 aper detected
Execute an INPUT check when there is paper at the position of the referenced sensor. 1: Paper not detected
Solution:
- Clean the sensor.
- Reconnect the connector.
- Replace the sensor.
- Replace the Paper Transport IOB.
- Replace the harness.
Checking paper jam, or paper status
Check if the leading edge of the paper and the paper feed guide are wet. If condensation has occurred inside the machine, leave the machine idle for a few minutes to remove condensation. Check if there is no double feeding. Fan the paper.
Check if the paper is curled too much.If the paper is curled too much, switch on the anti-condensation heater for paper tray. Check if extra thin paper or thick paper exceeding the supported paper thickness is being used. Use a supported paper type. Check if the paper thickness and size are detected correctly. Set the paper thickness and size to the correct value.
Troubleshooting
Reverse Sensor: Late Jam: Cause Code 024
Target Part/SP No.:Reverse Sensor / SP5-803-009 (Inverter Sensor)
Cause verification Problem Judgement Execute an INPUT check when there is no paper at the position of the referenced sensor. 0 aper detected
Execute an INPUT check when there is paper at the position of the referenced sensor. 1: Paper not detected
Solution:
- Clean the sensor.
- Reconnect the connector.
- Replace the sensor.
- Replace the Paper Transport IOB.
- Replace the harness.
Target Part/SP No.: Reverse Motor / SP5-804-047 (Inverter Motor:CW:Standard Speed)
Cause verification Problem Judgement Turn the referenced motor OFF with OUTPUT check Drive sound heard Turn the referenced motor ON with OUTPUT check Drive sound not heard
Solution:
- Reconnect the connector.
- Replace the motor.
- Replace the Paper Transport IOB.
- Replace the harness.
Target Part/SP No.
aper Exit Solenoid / SP5-804-004 (Exit Junction Solenoid)
Cause verification Problem Judgement Turn the referenced solenoid OFF with OUTPUT check Drive sound heard Turn the referenced solenoid ON with OUTPUT check Drive sound not heard
Solution:
- Reconnect the connector.
- Replace the solenoid.
- Replace the Paper Transport IOB.
- Replace the harness.
Checking paper jam, or paper status
Check if the leading edge of the paper and the paper feed guide are wet. If condensation has occurred inside the machine, leave the machine idle for a few minutes to remove condensation. Check if there is no double feeding. Fan the paper.
Check if the paper is curled too much.If the paper is curled too much, switch on the anti-condensation heater for paper tray. Check if extra thin paper or thick paper exceeding the supported paper thickness is being used. Use a supported paper type. Check if the paper thickness and size are detected correctly. Set the paper thickness and size to the correct value.
Troubleshooting
Reverse Sensor: Lag Jam : Cause Code 064
Target Part/SP No.:Reverse Sensor / SP5-803-009 (Inverter Sensor)
Cause verification Problem Judgement Execute an INPUT check when there is no paper at the position of the referenced sensor. 0 aper detected
Execute an INPUT check when there is paper at the position of the referenced sensor. 1: Paper not detected
Solution:
- Clean the sensor.
- Reconnect the connector.
- Replace the sensor.
- Replace the Paper Transport IOB.
- Replace the harness.
Target Part/SP No.
uplex Entrance Motor / SP5-804-065 (Duplex Entrance Motor:CW:Standard Speed)
Cause verification Problem Judgement Turn the referenced motor OFF with OUTPUT check Drive sound heard Turn the referenced motor ON with OUTPUT check Drive sound not heard
Solution:
- Clean the sensor.
- Reconnect the connector.
- Replace the sensor.
- Replace the Paper Transport IOB.
- Replace the harness.
Checking paper jam, or paper status
Check if the leading edge of the paper and the paper feed guide are wet. If condensation has occurred inside the machine, leave the machine idle for a few minutes to remove condensation. Check if there is no double feeding. Fan the paper.
Check if the paper is curled too much.If the paper is curled too much, switch on the anti-condensation heater for paper tray. Check if extra thin paper or thick paper exceeding the supported paper thickness is being used. Use a supported paper type. Check if the paper thickness and size are detected correctly. Set the paper thickness and size to the correct value.
Duplex Exit Sensor: Late Jam: Cause Code 025
Target Part/SP No.
uplex Exit Sensor / SP5-803-010
Cause verification Problem Judgement Execute an INPUT check when there is no paper at the position of the referenced sensor. 0 aper detected
Execute an INPUT check when there is paper at the position of the referenced sensor. 1: Paper not detected
Solution:
- Clean the sensor.
- Reconnect the connector.
- Replace the sensor.
- Replace the Paper Transport IOB.
- Replace the harness.
Target Part/SP No.: Bypass/Duplex Motor / SP5-804-071 (Duplex Bypass Motor:CW:Standard Speed)
Cause verification Problem Judgement Turn the referenced motor OFF with OUTPUT check Drive sound heard Turn the referenced motor ON with OUTPUT check Drive sound not heard
Troubleshooting
Solution:
- Reconnect the connector.
- Replace the motor.
- Replace the Paper Transport IOB.
- Replace the harness.
Checking paper jam, or paper status
Check if there is no double feeding. Fan the paper.
Check if the paper is curled too much.If the paper is curled too much, switch on the anti-condensation heater for paper tray. Check if extra thin paper or thick paper exceeding the supported paper thickness is being used. Use a supported paper type. Check if the paper thickness and size are detected correctly. Set the paper thickness and size to the correct value.
Duplex Exit Sensor: Lag Jam: Cause Code 065
Target Part/SP No.
uplex Exit Sensor / SP5-803-010
Cause verification Problem Judgement Execute an INPUT check when there is no paper at the position of the referenced sensor. 0 aper detected
Execute an INPUT check when there is paper at the position of the referenced sensor. 1: Paper not detected
Solution:
- Clean the sensor.
- Reconnect the connector.
- Replace the sensor.
- Replace the Paper Transport IOB.
- Replace the harness.
Checking paper jam, or paper status
Check if there is no double feeding. Fan the paper.
Check if the paper is curled too much.If the paper is curled too much, switch on the anti-condensation heater for paper tray. Check if extra thin paper or thick paper exceeding the supported paper thickness is being used. Use a supported paper type. Check if the paper thickness and size are detected correctly. Set the paper thickness and size to the correct value.
Duplex Entrance Sensor: Late Jam: Cause Code 027
Target Part/SP No.
uplex Entrance Sensor / SP5-803-011
Cause verification Problem Judgement Execute an INPUT check when there is no paper at the position of the referenced sensor. 0 aper detected
Execute an INPUT check when there is paper at the position of the referenced sensor. 1: Paper not detected
Solution:
- Clean the sensor.
- Reconnect the connector.
- Replace the sensor.
- Replace the Paper Transport IOB.
- Replace the harness.
Target Part/SP No.
uplex Entrance Motor / SP5-804-065 (Duplex Entrance Motor:CW:Standard Speed)
Cause verification Problem Judgement Turn the referenced motor OFF with OUTPUT check Drive sound heard Turn the referenced motor ON with OUTPUT check Drive sound not heard
Troubleshooting
Solution:
- Clean the sensor.
- Reconnect the connector.
- Replace the sensor.
- Replace the Paper Transport IOB.
- Replace the harness.
Target Part/SP No.
aper Exit Solenoid / SP5-804-004 (Exit Junction Solenoid)
Cause verification Problem Judgement Turn the referenced solenoid OFF with OUTPUT check Drive sound heard Turn the referenced solenoid ON with OUTPUT check Drive sound not heard
Solution:
- Reconnect the connector.
- Replace the solenoid.
- Replace the Paper Transport IOB.
- Replace the harness.
Checking paper jam, or paper status
Check if there is no double feeding. Fan the paper.
Check if the paper is curled too much.If the paper is curled too much, switch on the anti-condensation heater for paper tray. Check if extra thin paper or thick paper exceeding the supported paper thickness is being used. Use a supported paper type. Check if the paper thickness and size are detected correctly. Set the paper thickness and size to the correct value. Duplex Entrance Sensor: Lag Jam: Cause Code 067
Target Part/SP No.
uplex Entrance Sensor / SP5-803-011
Cause verification Problem Judgement Execute an INPUT check when there is no paper at the position of the referenced sensor. 0 aper detected
Execute an INPUT check when there is paper at the position of the referenced sensor. 1: Paper not detected
Solution:
- Clean the sensor.
- Reconnect the connector.
- Replace the sensor.
- Replace the Paper Transport IOB.
- Replace the harness.
Target Part/SP No.
uplex Entrance Motor/ SP5-804-065 (Duplex Entrance Motor:CW:Standard Speed)
Cause verification Problem Judgement Turn the referenced motor OFF with OUTPUT check Drive sound heard Turn the referenced motor ON with OUTPUT check Drive sound not heard
Solution:
- Reconnect the connector.
- Replace the sensor.
- Replace the Paper Transport IOB.
- Replace the harness.
Target Part/SP No.
uplex/ Bypass Motor / SP5-804-071 (Duplex Bypass Motor:CW:Standard Speed)
Cause verification Problem Judgement Turn the referenced motor OFF with OUTPUT check Drive sound heard Turn the referenced motor ON with OUTPUT check Drive sound not heard
Troubleshooting
Solution:
- Reconnect the connector.
- Replace the sensor.
- Replace the Paper Transport IOB.
- Replace the harness.
Checking paper jam, or paper status
Check if there is no double feeding. Fan the paper.
Check if the paper is curled too much.If the paper is curled too much, switch on the anti-condensation heater for paper tray. Check if extra thin paper or thick paper exceeding the supported paper thickness is being used. Use a supported paper type. Check if the paper thickness and size are detected correctly. Set the paper thickness and size to the correct value. Duplex No Feeding: Cause Code 009
Target Part/SP No.:Registration Sensor / SP5-803-001 (Registration Sensor)
Cause verification Problem Judgement Execute an INPUT check when there is no paper at the position of the referenced sensor. 0 aper detected
Execute an INPUT check when there is paper at the position of the referenced sensor. 1: Paper not detected
Solution:
- Clean the sensor.
- Reconnect the connector.
- Replace the sensor.
- Replace the Paper Transport IOB.
- Replace the harness.
Checking paper jam, or paper status
Check if there is no double feeding. Fan the paper.
Check if the paper is curled too much.If the paper is curled too much, switch on the anti-condensation heater for the paper tray. Check if extra thin paper or thick paper exceeding the supported paper thickness is being used. Use a supported paper type. Check if the paper thickness and size are detected correctly. Set the paper thickness and size to the correct value.
Troubleshooting
Bypass Transport Sensor 1: Lag Jam: Cause Code 048
Target Part/SP No.:Transport Sensor (1st Feed Tray) / SP5-803-003 (Transport Sensor 1)
Cause verification Problem Judgement Execute an INPUT check when there is no paper at the position of the referenced sensor. 0 aper detected
Execute an INPUT check when there is paper at the position of the referenced sensor. 1: Paper not detected
Solution:
- Clean the sensor.
- Reconnect the connector.
- Replace the sensor.
- Replace the Paper Transport IOB.
- Replace the harness.
Target Part/SP No.: Transport Motor / SP5-804-028 (Bypass V-Transport Motor: CW: Std Speed)
Cause verification Problem Judgement Turn the referenced motor OFF with OUTPUT check Drive sound heard Turn the referenced motor ON with OUTPUT check Drive sound not heard
Solution:
- Reconnect the connector.
- Replace the motor.
- Replace the Paper Transport IOB.
- Replace the harness.
DISPLAY ERROR
"No paper in Tray 1" is displayed even when the paper is in
Target Part/SP No.
aper End Sensor (1st Feed Tray) / SP5-803-015 (Tray 1: Paper End Detection)
Cause verification Problem Judgement Execute an INPUT check when there is no paper at the position of the referenced sensor. 1: Paper detected Execute an INPUT check when there is paper at the position of the referenced sensor. 0: Paper not detected
Solution:
- Reconnect the connector.
- Replace the sensor.
- Replace the Paper Transport IOB.
- Replace the harness.
Feeler for 1st paper end sensor
Cause verification Problem Judgement Check if the feeler for 1st paper end sensor is unfastened. Feeler is unfastened.
Solution:
- Reinstall the feeler.
- Check if there are any defects in the 1st paper feed unit.
"No paper in Tray 2" is displayed even when the paper is in
Target Part/SP No.
aper End Sensor (2nd Feed Tray) / SP5-803-019 (Tray 2: Paper End Detection)
Cause verification Problem Judgement Execute an INPUT check when there is no paper at the position of the referenced sensor. 1: Paper detected Cause verification Problem Judgement Execute an INPUT check when there is paper at the position of the referenced sensor. 0: Paper not detected
Troubleshooting
Solution:
- Reconnect the connector.
- Replace the sensor.
- Replace the Paper Transport IOB.
- Replace the harness.
Feeler for 2nd paper end sensor
Cause verification Problem Judgement Check if the feeler for 2nd paper end sensor is unfastened. Feeler is unfastened.
Solution:
- Reinstall the feeler.
- Check if there are any defects in the 2nd paper feed unit.
"Tray 1 not set" is displayed even when the tray is set
Target Part/SP No.:Tray Set Switch (1st Feed Tray) / SP5-803-016 (Tray 1: Set Sensor)
Cause verification Problem Judgement Manually press the referenced switch (Done after detaching paper feeding tray 1 from the machine.) 1: Not set Pull out paper feed tray 1 from the machine. 0: Set
Solution:
- Reconnect the connector.
- Replace the sensor.
- Replace the Paper Transport IOB.
- Replace the harness.
1st Paper Feed Tray
Replace the 1st paper feed tray. Replace the 1st paper feed tray. "Tray 2 not set" is displayed even when the tray is set
Target Part/SP No.:Tray Set Switch (2nd Feed Tray) / SP5-803-020 (Tray 2: Set Sensor)
Cause verification Problem Judgement Manually press the referenced switch (Done after detaching paper feeding tray 2 from the machine.) 1: Not set Pull out paper feed tray 2 from the machine. 0: Set
Solution:
- Reconnect the connector.
- Replace the sensor.
- Replace the Paper Transport IOB.
- Replace the harness.
2nd Paper Feed Tray
Check the 2nd tray set sensor to see if there are any defects. Replace the 2nd paper feed tray.
Wrong paper size displayed on the operation panel
Target Part/SP No.:Size Switch (2nd Feed Tray) / SP5-803-021 (Tray 2: Size Sensor)
Cause verification Problem Judgement Press the 1st switch from the right on the size switch of paper feed tray 2 when seen from the front of the machine (Done after detaching paper feed tray 2) Parameter other than 00000111 Press the 2nd switch from the right on the size switch of paper feed tray 2 when seen from the front of the machine (Done after detaching paper feed tray 2) Parameter other than 00001011 Press the 3rd switch from the right on the size switch of paper feed tray 2 when seen from the front of the machine (Done after detaching paper feed tray 2) Parameter other than 00001101 Cause verification Problem Judgement Press the 4th switch from the right on the size switch of paper feed tray 2 when seen from the front of the machine (Done after detaching paper feed tray 2) Parameter other than 00001110 Pull out paper feed tray 2 from the machine. Parameter other than 00001111
Troubleshooting
Solution:
- Reconnect the connector.
- Replace the sensor.
- Replace the Paper Transport IOB.
- Replace the harness.
Replace the switch for the pick-up arm.
2nd Paper Feed Tray
Check the 2nd tray set sensor to see if there are any defects.
Does not shift to right door open status
Target Part/SP No.:Right Door Open/Close Switch / SP5-803-026 (Right Door Open/Close Sensor)
Cause verification Problem Judgement Manually press the referenced switch (Done after opening the right door) 1: Open Open the right door 0: Close
Solution:
- Reconnect the connector.
- Replace the sensor.
- Replace the Paper Transport IOB.
- Replace the harness.
Target Part/SP No.
uplex Unit Open/Close Sensor / SP5-803-027 (Tray Full Exit Sensor)
Cause verification Problem Judgement Manually press the referenced switch (Done after opening the duplex guide plate) 1: Open Open the duplex guide plate. 0: Close
Solution:
- Reconnect the connector.
- Replace the sensor.
- Replace the Paper Transport IOB.
- Replace the harness.
Replace the 2nd paper feed tray.
Pick-up Arm
Check the switch for the pick-up arm to see if there are any defects.
OTHERS
- If the error occurs periodically, do the following steps. If the result is as shown in the "Problem Judgement" column, follow the solutions.
"Replace the waste toner bottle" is displayed even when it is clear that the waste toner bottle is not full
Target Part/SP No.: Waste Toner Bottle Full Sensor / SP5-803-032 (Toner Collection Full Sensor)
Cause verification Problem Judgement Execute an INPUT check with no feeler in the sensor detection range (Done after detaching the waste toner bottle) 1: Full
Solution:
- Clean the sensor.
- Reconnect the connector.
- Replace the sensor.
- Replace the Imaging IOB.
- Replace the harness.
Troubleshooting
Waste toner bottle is never full
Target Part/SP No.: Waste Toner Bottle Full Sensor / SP5-803-032 (Toner Collection Full Sensor)
Cause verification Problem Judgement Execute an INPUT check with feeler within the sensor detection range (Done after removing the waste toner bottle) 0: Not full
Solution:
- Clean the sensor.
- Reconnect the connector.
- Replace the sensor.
- Replace the Imaging IOB.
- Replace the harness.
No waste toner bottle set is displayed on controller board even when it is clear that is set
Target Part/SP No.:Waste Toner Bottle Set Sensor / SP5-803-033 (Toner Collection Bottle Set Sensor)
Cause verification Problem Judgement Execute an INPUT check with the feeler within the sensor detection range (Done after removing the waste toner bottle) 1: Not set
Solution:
- Reconnect the connector.
- Replace the sensor.
- Replace the Imaging IOB.
- Replace the harness.
Waste toner bottle is not detected even when it is set
Target Part/SP No.:Waste Toner Bottle Set Sensor / SP5-803-033 (Toner Collection Bottle Set Sensor)
Cause verification Problem Judgement Detach the waste toner bottle from the machine. 0: Set
Solution:
- Reconnect the connector.
- Replace the sensor.
- Replace the Imaging IOB.
- Replace the harness.
Paper transfer unit open/close LED not lit and paper transfer unit open
Target Part/SP No.
TR Open/Close Sensor / SP5-803-028 (PTR Open/Close Sensor)
Cause verification Problem Judgement Execute an INPUT check with an object (e.g. paper) placed within the sensor detection range. 1: Close Execute an INPUT check without an object (e.g. paper) placed within the sensor detection range. 0: Open
Solution:
- Clean the sensor.
- Reconnect the connector.
- Replace the sensor.
- Replace the Paper Transport IOB.
- Replace the harness.
Paper transfer unit open/close LED not lit
Target Part/SP No.
aper Transfer Unit Open/Close LED / SP5-804-206 (PTR Open/Close LED)
Cause verification Problem Judgement Turn ON the paper transfer unit open/close LED with OUTPUT check 1: Close Execute an OUTPUT check without an object (e.g. paper) placed within the sensor detection range. 0: Open
Solution:
- Clean the LED.
- Reconnect the connector.
Troubleshooting
- Replace the LED.
- Replace the Paper Transport IOB.
- Replace the harness.
Paper transfer unit open/close LED always lit
Target Part/SP No.
TR Open/Close Sensor / SP5-803-028 (PTR Open/Close Sensor)
Cause verification Problem Judgement Execute an INPUT check with an object (e.g. paper) placed within the sensor detection range 1: Close Execute an INPUT check without an object (e.g. paper) placed within the sensor detection range 0: Open
Solution:
- Clean the sensor.
- Reconnect the connector.
- Replace the sensor.
- Replace the Paper Transport IOB.
- Replace the harness.
Target Part/SP No.
aper Transfer Unit Open/Close LED / SP5-804-206 (PTR Open/Close LED)
Cause verification Problem Judgement Turn OFF the paper transfer unit open/close LED with OUTPUT check LED lit
Solution:
- Clean the LED.
- Reconnect the connector.
- Replace the LED.
- Replace the Paper Transport IOB.
- Replace the harness.
TROUBLESHOOTING FOR FINISHING OPTIONS
FINISHER REGISTRATION ADJUSTMENT FOR BOOKLET FINISHER SR3220 (D3B9)
Side-to-side registration can be adjusted by the docking bracket for SR3220 [A] (and the docking bracket screw ).
Eject a sheet of A4(LEF) or A3 paper to the proof tray and check for how many divisions of the scale the edge of the paper has shifted from the center.
[A]: Scale marks for DLT : Scale marks for A3
[C]: 7 scale marks in 2mm intervals [D]: Center mark
[*]Change the position of the standard bracket by rotating it 180 degrees as shown below.
Troubleshooting
This makes the docking bracket easier to slide horizontally. Then reattach the docking bracket to the mainframe.
[A]: Reverse
If the paper shifts towards the front
Slide the docking bracket towards the front side by the amount of shift, to move the finisher in the same direction.
e.g.: When the paper has shifted by 2 mm towards the front from the center mark (2 mm/division of the scale), move the docking bracket towards the front by 2 mm (2 divisions). The divisions move towards the rear.
[A]: Proof Tray
: Docking Bracket Screw
If the paper shifts towards the rear
Slide the docking bracket towards the rear by the amount of shift, to move the finisher in the same direction.
e.g.: When the paper has shifted by 2 mm towards the rear from the center mark (2 mm/division of the scale), move the docking bracket towards the rear by 2 mm (2 divisions). The divisions move towards the front.
[A]: Proof Tray
: Docking Bracket Screw
- After the adjustment, check the side-to-side registration by feeding paper out to the proof tray. If the shift has not been solved, adjust the docking bracket (screw for the docking bracket) slightly again.
[*]FINISHER JOGGER PROBLEM (FOR BOOKLET FINISHER SR3220 (D3B9)
If a paper alignment problem occurs as shown below, do the following procedure to adjust the jogger width.
Cause
Depending on the type of paper or the manufacturer, the paper may not be the correct size. In this case, the paper may not align properly even when the jogger is used.
Solution
Adjust the jogger width with SP6-143 (adjustable threshold: -1.5 to +1.5 mm for each paper size).
- SP6-143 (Jogger Pos Adj:1K FIN)
- Adjust the jogger width to be slightly narrower (approximately -0.5 mm) than the paper width.
Troubleshooting
- Adjust the jogger width to be slightly narrower (approximately -0.5 mm) than the paper width.
EARLY TRAY FULL DETECTION MYLAR FOR INTERNAL FINISHER SR3130 (D690)
Paper curl may occur when output gets to near full. Paste the Mylar to the full detection feeler to detect tray full early before paper curl occurs.
Pasting the Mylar
Pull the finisher [A]
Remove the finisher front cover [A]
Remove the left lower cover [A]
Rotate the gear [A] to lift down the movable tray .
[*]Remove the paper exit tray [A]
[*]Paste the Mylar [A] on the full detection feeler .
Troubleshooting
[*]Re-attach the paper exit tray
[*]Move the movable tray [A] up and down to check that the Mylar does go through the sensor properly.
[*]Re-attach the left lower cover
[*]Re-attach the finisher front cover
[*]PAPER CURL PROBLEM FOR SR3180 (D766)
When using the mixed mode, duplex (curls towards the lower side) over the simplex (curl towards the upper side) and paper curl occurs, attach the auxiliary tray (D7667010), disable the paper exit full sensor, and paste the Mylar.
Remove the paper exit cover [A]
Release the clamp and disconnect the harness of the paper exit full sensor 1 [A].
Loop and clamp the harness [A] as shown.
Release the clamp and disconnect the harness of the paper exit full sensor 2 (Staple) [A].
Troubleshooting
Loop and clamp the harness [A] as shown.
- If the harness cable [A] is short to loop, clamp the harness without looping.
- If the harness cable [A] is short to loop, clamp the harness without looping.
Re-attach the paper exit cover ( ×2)
Attach the auxiliary tray (D7667010) to the paper exit tray [A]
[*]Paste the Mylars [A] on the frame of the finisher.
[*]
[*]MAXIMUM NUMBER OF SHEETS FOR STAPLING AND WHAT HAPPENS WHEN THE JOB HAS TOO MANY PAGES
Specifications: Maximum sheet capability for staple jobs
Model Corner Staple Booklet Staple Booklet Finisher SR3220 50 sheets 15 sheets Internal Finisher SR3130 50 sheets -
Behavior: When the number of sheets exceeds the maximum staple capability
When corner stapling
Sheets are fed out without being stapled. First, the maximum number of sheets (50) is stacked in the staple tray and fed out. Following this, any remaining sheets that exceed this maximum are also stacked and fed out without being stapled, in the same way.
Example:
If 60 sheets are set to be stapled, the first 50 are stacked in the staple tray and then fed out without being stapled. The remaining 10 are then stacked in the tray and fed out without being stapled.
When the maximum number of originals for a stapled set has been scanned, "Stapling capacity exceeded" is displayed on the LCD.
Troubleshooting
There is no message displayed prompting the user to cancel or continue with the 51st original.
When booklet stapling
The following dialog is displayed when the maximum number of sheets in a stapled set is reached during the scanning of the originals. The user is prompted before printing begins.
[Stop] The job is canceled (no further scanning, no printing)
[Continue] Sets are stapled at maximum capacity in batch and fed out. Example:
The machine stops scanning after 20 out of 30 originals are scanned. The message shown above is displayed.
If [Continue] is selected, printing starts and sheets are stapled in batches of 20 sheets and 10 sheets.
Select the behavior when the job has more than the maximum of staple capability with SP5199
SP5-199 sets whether to staple sheets stacked in the staple tray or finisher before feeding out. 0 (default): Behavior depends on the finisher attached.
1: Sheets are fed out without being stapled. 2: Sheets are stapled and fed out.
6.17 ELECTRICAL COMPONENT DEFECTS
6.17.1 FUSES
Name
Output connector
Capacity
Part numberMarket exchange possible Voltage Part name Remarks
FU101
CN985 (Fusing center lamp)
CN986 (Fusing edge lamp)15A (NA)
8A11071241(NA)
11071366
Yes
ACTLC-15A-N4 (NA)
FIH 250V 8A(EM)8A
Installed on AC control board
FU102
CN988 (DC power supply)15A(NA)
8A11071241(NA)
11071366
Yes
ACTLC-15A-N4 (NA)
FIH 250V 8A(EM)8A
Installed on AC control board
FU110CN921(Heater for Tray1, 2, and optional trays) CN922 (Heater for Scanner and PCU) 2A 11071225 NO
AC
SLT 250V 2A
Installed on Heater Board (Service Part)
FU105
None2A 11071362 NO
AC
SCT2AInstalled on AC control board
FU1
CN911(IOB)5A 11071229 NO
5V
SLT 250V 5AInstalled on DC power supply FU2 CN911(IPU) 5A 11071229 NO
Name
Output connector
Capacity
Part numberMarket exchange possible Voltage Part name Remarks
5V
SLT 250V 5AInstalled on DC power supply
FU3
CN912(IOB)8A NO
24V
51MS(P)080LInstalled on DC power supply
FU4
CN917 (Interlock switch [IOB])8A NO
24V
51MS(P)080LInstalled on DC power supply
FU5
CN917 (Interlock switch [IOB])8A NO
24V
51MS(P)080LInstalled on DC power supply
FU7
CN913(FIN) CN914(BANK)8A NO
24V
51MS(P)080LInstalled on DC power supply
Troubleshooting
Fuse position
Troubleshooting
6.18 VERTICAL STREAKS ON COPIES DUE TO SCANNING PROBLEMS
6.18.1 OVERVIEW
Marks on prints and copies are mostly due to dirt on the DF exposure glass [A], generally caused by adhesive contaminants (such as ball point pen ink and correction fluid).
Compared to non-adhesive contaminants (such as paper fragments and eraser dust), adhesive contaminants are more likely to lead to complaints from customers because of the following:
[*]Vertical streaks caused by adhesive contaminants are more visible in terms of image quality.
[*]Unless removed by cleaning, adhesive contaminants continue to produce vertical streaks, while non-adhesive contaminants stop producing streaks after they are dislodged.
[*]Many adhesive contaminants are difficult to remove by cleaning.
The ARDF DF3090 / SPDF DF3100 features a system (non-contact scanning) to reduce vertical streaks caused by adhesive contaminants.
Contact scanning: Other ADFs/ARDFs | Non-contact scanning: DF3090 / DF3100 |
In contact scanning, the whole of the original comes into contact with the DF exposure glass [A] so that non-adhesive contaminants can be removed.![]() | By means of the Mylar sheet , originals are kept slightly above the DF exposure glass [A], preventing adhesive contaminants from adhering to the glass. |
The ARDF DF3090 / SPDF DF3100 can be converted from non-contact scanning to contact
scanning for users who wish to reduce vertical streaks caused by non-adhesive contaminants.
SP No. | Contact scanning | Non-contact scanning |
SP4-688-001 (for ARDF3090) | 103% | 106% |
SP4-688-002 (for SPDF3100) | 96% | 101% |
SP4-871-003 (both ARDF and SPDF) | 0.00% | 0.11% |
Converting the ARDF DF3090 to Contact Scanning
Unplug the machine power cord before starting the following procedure.
Remove the ARDF front cover [A] (
Remove the Scanning guide plate
[*]Remove the plastic guides [A] on the sides of the scanning guide
Troubleshooting
[*]Attach the guides for contact scanning. Each guide has a hole .
[*]Mount the scanning guide plate, taking care not to damage the sheet [A].
[*]Peel off the gap sheet [A] from the DF exposure glass with your hands.
[*]Clean the DF exposure glass [A] with alcohol.
To avoid paper jams, make sure adhesive is completely removed.
[*]Turn the main switch on.
[*]Start the SP mode.
[*]Select SP4-688-001 (DF Density Adjustment ARDF) and change the setting from "106" to "103" for the contact scanning.
[*]Change the DF magnification (SP4-871-003) from [0.11%] to [0.00%].
- When returning the setting back to non-contact scanning, return the SP values also.
Converting the SPDF3100 to Contact Scanning
Open the SPDF and exchange the entrance lower guide unit [A] to a non-contact type part.
- Entrance lower guide unit for non-contact transport: The following areas are black [A].
- Entrance lower guide unit for contact transport: The following areas are clear and colorless .
Troubleshooting
[*]Exchange the scanning guide plate [A] to a non-contact type part (hook x 1).
- [A] : The color of the marker of the non-contact type scanning guide plate for this machine is gray.
- : The color of the marker of the contact type scanning guide plate for this machine is white.
[*][C]: The color of the marker of the non-contact type scanning guide plate for previous machine is black.
[*]Attach the scanning guide plate for contact transport [A] (hook x 1).
[*]Attach the entrance lower guide unit for contact transport
[*]Peel off the gap sheet [A] from the DF exposure glass with your hands.
[*]Clean the DF exposure glass [A] with alcohol.
To avoid paper jams, make sure adhesive is completely removed.
[*]Enter the SP mode.
[*]Change SP4-688-002 (Scan Image Density Adjustment 1-pass) from "101" to "96".
[*]Change the DF magnification (SP4-871-003) from [0.11%] to [0.00%].
- When returning the setting back to non-contact scanning, return the SP values also.
Troubleshooting
IMAGE QUALITY PROBLEMS
MISJUDGMENT FOR AUTO COLOR SELECTION (COPY/SCANNER)
In the Auto Color Selection (hereafter called ACS) mode, if copying or scanning an original on which color is printed only on the edge, the original will be misjudged as monochrome. If so, color is not printed on the output.
Error Condition
Copy Application
The misjudgment occurs when copying an original which has color at the edge, and that color is printed on the output 10 mm from the edge in the ACS mode.
When using the copy application, if the original is judged as monochrome, color on the document may not be printed on the output. When printing the standard 10 colors used in Microsoft Office Word 2013 (an example is shown below), the following colors with the "x" mark will disappear if the document is judged as monochrome in the ACS mode.
- Colors with the "x" mark will not be printed if the document is judged as monochrome. The result may differ depending on the equipment status or environment.
Scanner Application
The misjudgment occurs when scanning an original which has color only 15 mm from the edge (using the original as a standard) in the ACS mode.
Causes
In the ACS mode, the edge of the original is excluded from the judgment. Only the center part of the original document is the target area to judge color or monochrome (in order to prevent misjudgment due to noise).
When copying in the ACS mode, ACS judgment and the image processing equivalent to full color is performed simultaneously. If judged as monochrome in the ACS judgment, color without a K component will not be printed.
Solutions
Change the ACS area excluded from judgment with the following SP settings.
The smaller the value, the smaller the ACS area excluded from judgment becomes, which enables the document to be judged as color.
SP No. SP Name Def. Max. Min. 4-938-001 ACS:Edge Mask Copy:Sub LEdge 10 0 31 4-938-002 ACS:Edge Mask Copy:Sub TEdge 10 0 31 4-938-003 ACS:Edge Mask Copy:Main LEdge 10 0 31 4-938-004 ACS:Edge Mask Copy:Main TEdge 10 0 31 4-938-005 ACS:Edge Mask Scan:Sub LEdge 15 0 31 4-938-006 ACS:Edge Mask Scan:Sub TEdge 15 0 31 4-938-007 ACS:Edge Mask Scan:Main LEdge 15 0 31 4-938-008 ACS:Edge Mask Scan:Main TEdge 15 0 31
[A]: Sub scan direction: leading edge (left) : Main scan direction (front)
[C]: Sub scan direction: leading edge (right)
Troubleshooting
[D]: Main scan direction (rear) [E]: Paper
[F]: ACS area excluded from judgment
- Because the edge of the original is subject to noise, color misjudgment may occur after setting these SPs smaller than the defaults. In this case, in order to avoid complaints concerning extra cost, be sure to ask the customer for permission before changing these SP settings.
[*]MISJUDGMENT FOR AUTO COLOR SELECTION (E.G. WHEN USING PAPER WHICH HAS A STRONG BLUE COMPONENT)
Causes
The strong blue component of the paper causes the difference in RGB values to be relatively large. As a result, ACS mistakenly judges that the paper is blue.
- ACS makes this judgment based on the RGB thresholds set in SP mode.
Solutions
Change the setting of SP4-939-001 (ACS:Color Range) until ACS works correctly.
- Change the value of the SP to “-1” or “-2” when a black and white document is misjudged as a color document.
WHEN AN ABNORMAL IMAGE IS GENERATED
- Colors with the "x" mark will not be printed if the document is judged as monochrome. The result may differ depending on the equipment status or environment.
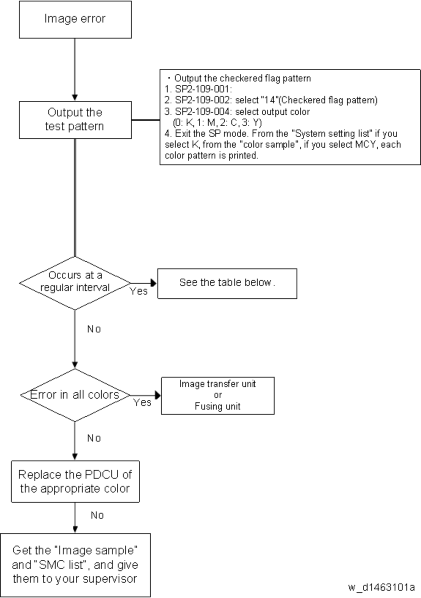
Troubleshooting
Interval | Target part | Replacement part |
31.4mm | Charge roller cleaner | PCU |
34.6mm | Development roller | Development unit |
37.7mm | Charge roller | PCU |
48.7mm | Paper transfer roller | Paper transfer roller unit |
54.8mm | Image transfer drive roller | Image transfer unit |
94.2mm | Drum | PCU |
94.2mm | Fusing sleeve belt | Fusing sleeve belt unit/ Fusing unit |
100.5mm | Pressure roller | Pressure roller/ Fusing unit |
963.8mm | Image transfer belt | Image transfer belt/ Image transfer unit |
6.20 OTHER TROUBLESHOOTING
6.20.1 WHEN FLUORESCENT/ LED LAMPS FLICKER
Problem
Under the usage environment of this machine, at the placement location, fluorescent and/or LED lamps flicker.Causes
As a result of the voltage drop occurs, when the fusing lamp is applied an electrical current. It depends on the electrical power environment, at the customer's placement location.Solutions
The procedure varies by the flicker occurrence timing. So check the occurrence timing, and do the procedure that matches the timing.Occurrence Timing
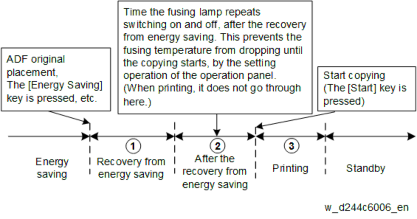
Timing | Solutions | Side effect |
![]() | Set SP1-135-001 (Inrush Control) to "1 (ON)". | Recovery time from energy saving becomes slower approx. 0.4 sec.. |