
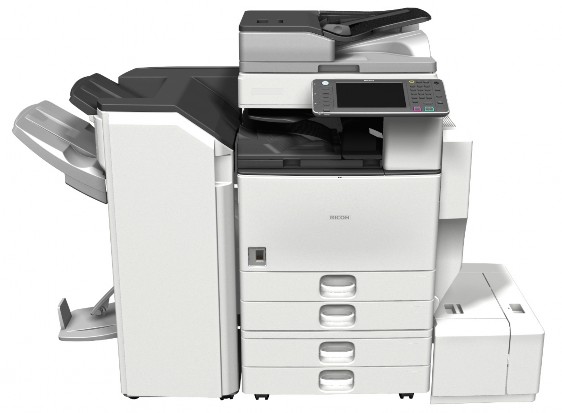
D129/D130 SERVICE MANUAL

It is the reader's responsibility when discussing the information contained within this document to maintain a level of confidentiality that is in the best interest of Ricoh Americas Corporation and its member companies.
NO PART OF THIS DOCUMENT MAY BE REPRODUCED IN ANY FASHION AND DISTRIBUTED WITHOUT THE PRIOR PERMISSION OF RICOH AMERICAS CORPORATION.
All product names, domain names or product illustrations, including desktop images, used in this document are trademarks, registered trademarks or the property of their respective companies.
They are used throughout this book in an informational or editorial fashion only and for the benefit of such companies. No such use, or the use of any trade name, or web site is intended to convey endorsement or other affiliation with Ricoh products.
2012 RICOH Americas Corporation. All rights reserved.
WARNING
The Service Manual contains
regarding service techniques,
information procedures,
processes and spare parts of office equipment distributed by Ricoh Americas Corporation. Users of this manual should be either service trained or certified by successfully completing a Ricoh Technical Training Program.
Untrained and uncertified users utilizing information contained in this service manual to repair or modify Ricoh equipment risk personal injury, damage to property or loss of warranty protection.
Ricoh Americas Corporation
LEGEND
PRODUCT CODE | COMPANY | ||
LANIER | RICOH | SAVIN | |
D129-17 | MP 4002 | Aficio MP 4002 | MP 4002 |
D129-57 | MP 4002SP | Aficio MP 4002SP | MP 4002SP |
D130-17 | MP 5002 | Aficio MP 5002 | MP 5002 |
D130-57 | MP 5002SP | Aficio MP 5002SP | MP 5002SP |
DOCUMENTATION HISTORY
REV. NO. | DATE | COMMENTS |
* | 01/2012 | Original Printing |
D129/D130
TABLE OF CONTENTS
- PRODUCT INFORMATION 1-1
- SPECIFICATIONS 1-1
- MACHINE CONFIGURATION 1-2
- COPIER 1-2
- GUIDANCE FOR THOSE WHO ARE FAMILIAR WITH PREDECESSOR PRODUCTS 1-5
- OVERVIEW 1-6
- COMPONENT LAYOUT 1-6
- PAPER PATH 1-8
- DRIVE LAYOUT 1-9
- INSTALLATION 2-1
- INSTALLATION REQUIREMENTS 2-1
- ENVIRONMENT 2-2
- MACHINE LEVEL 2-2
- MINIMUM SPACE REQUIREMENTS 2-3
- POWER REQUIREMENTS 2-3
- INSTALLATION FLOW CHART 2-4
- MAIN MACHINE INSTALLATION 2-5
- ACCESSORY CHECK 2-5
- INSTALLATION PROCEDURE 2-7
Preliminary Procedures 2-7
PCDU (Photoconductor and Development Unit) 2-10
Toner Bottle 2-13
Paper Trays 2-13
Initialize TD Sensor and Developer 2-14
Set Paper Size for Paper Trays 2-14
Electrical Total Counter 2-14
Exposure Glass Cleaner 2-15
Settings Relevant to the Service Contract 2-15
Data Overwrite Security 2-16
HDD Encryption 2-17
App 2 Me Setting (SP model only) 2-18 - MOVING THE MACHINE 2-19
- TRANSPORTING THE MACHINE 2-19
- PAPER FEED UNIT INSTALLATION (D580) 2-20
- ACCESSORY CHECK 2-20
- INSTALLATION PROCEDURE 2-20
- 2000-SHEET LCT INSTALLATION (D581) 2-23
- ACCESSORY CHECK 2-23
- INSTALLATION PROCEDURE 2-23
- 1200-SHEET LCT INSTALLATION (D631) 2-26
- COMPONENT CHECK 2-26
- INSTALLATION PROCEDURE 2-27
- ARDF INSTALLATION (D630) 2-29
- COMPONENT CHECK 2-29
- INSTALLATION PROCEDURE 2-29
- 1-BIN TRAY UNIT INSTALLATION (D632) 2-33
- COMPONENT CHECK 2-33
- INSTALLATION PROCEDURE 2-34
- BRIDGE UNIT INSTALLATION (D634) 2-36
- COMPONENT CHECK 2-36
- INSTALLATION PROCEDURE 2-37
2.10 3000/2000-SHEET (BOOKLET) FINISHER (D636/D637) 2-41- ACCESSORY CHECK 2-41
- INSTALLATION PROCEDURE 2-42
Support Tray Installation 2-45
- PUNCH UNIT INSTALLATION (D570) 2-46
- COMPONENT CHECK 2-46
- INSTALLATION PROCEDURE 2-47
- PLATEN COVER (D593) 2-52
2.14 SIDE TRAY (D635) 2-57- ACCESSORY CHECK 2-53
- INSTALLATION PROCEDURE 2-54
- COMPONENT CHECK 2-57
- INSTALLATION PROCEDURE 2-58
- INTERNAL SHIFT TRAY (D633) 2-62
- COMPONENT CHECK 2-62
- INSTALLATION PROCEDURE 2-62
Rev. 04/23/2012
- KEY COUNTER INSTALLATION 2-64
- INSTALLATION PROCEDURE 2-64
- KEY COUNTER INTERFACE UNIT INSTALLATION 2-66
- INSTALLATION PROCEDURE 2-66
- TRAY HEATER 2-68
- INSTALLATION PROCEDURE 2-68
- TRAY HEATER (OPTIONAL PAPER FEED UNIT) 2-70
- COMPONENT CHECK 2-70
- INSTALLATION PROCEDURE 2-71
For installing the tray heater in the D580 (Two-tray paper feed unit) . 2-71 For installing the tray heater in the D581 (LCT) 2-73
- HDD INSTALLATION (D640-11) 2-76
- COMPONENT CHECK 2-76
- INSTALLATION PROCEDURE 2-77
After Installing the HDD 2-78
- COPY DATA SECURITY UNIT (B829) 2-79
- COMPONENT CHECK 2-79
- INSTALLATION PROCEDURE 2-80
User Tool Setting 2-81
Check All Connections 2-82
- BROWSER UNIT TYPE I 2-83
- INSTALLATION PROCEDURE 2-83
- UPDATE PROCEDURE 2-85
- CARD READER BRACKET TYPE C3352 (D593) 2-87
- COMPONENT CHECK 2-87
- INSTALLATION PROCEDURE 2-88
- INSTALLATION REQUIREMENTS 2-1
- PREVENTIVE MAINTENANCE 3-1
- PM TABLES 3-1
- REPLACEMENT AND ADJUSTMENT 4-1
- GENERAL CAUTIONS 4-1
- LASER UNIT 4-1
- USED TONER 4-1
- SPECIAL TOOLS AND LUBRICANTS 4-2
- SPECIAL TOOLS 4-2
- LUBRICANTS 4-2
- EXTERIOR COVERS 4-3
- FRONT DOOR, UPPER AND LOWER INNER COVER 4-3
SM iii D129/D130
Rev. 09/11/2012
Upper Inner Cover 4-3
Lower Inner Cover 4-3 - LEFT COVER 4-4
- REAR COVER 4-4
- RIGHT REAR COVER 4-5
- FRONT RIGHT COVER 4-6
- OPERATION PANEL & LCD 4-6
- PAPER EXIT COVER 4-10
- INNER TRAY 4-11
- FRONT DOOR, UPPER AND LOWER INNER COVER 4-3
- SCANNER 4-12
- EXPOSURE GLASS 4-12
- SCANNER EXTERIOR PANELS AND OPERATION PANEL 4-12
Operation panel 4-12
Scanner left cover 4-12
Scanner right cover 4-13
Scanner front cover 4-13
Scanner rear cover 4-13 - LENS BLOCK ASSEMBLY 4-14
When reassembling 4-15 - ORIGINAL SIZE SENSOR 4-15
- EXPOSURE LAMP 4-17
Chromaticity rank adjustment 4-18 - SCANNER HP SENSOR/PLATEN COVER SENSOR. 4-20
Scanner HP Sensor 4-20
Platen Cover Sensor 4-21 - SCANNER MOTOR 4-22
- SCANNER MOTOR DRIVE BOARD 4-24
- FRONT SCANNER WIRE 4-24
Reassembling the Front Scanner Wire. 4-26 - REAR SCANNER WIRE 4-29
Reassembling the Rear Scanner Wire 4-30
- LASER UNIT 4-31
- CAUTION DECAL LOCATIONS 4-31
- LASER UNIT 4-31
- POLYGON MIRROR MOTOR 4-33
- LASER SYNCHRONIZATION DETECTOR 4-33
- LD UNIT 4-34
Laser Beam Pitch Adjustment 4-34
D129/D130 iv SM
4.6 PCDU 4-37
4.6.1 PCDU (PHOTOCONDUCTOR AND DEVELOPMENT UNIT) 4-37
Reinstallation 4-37
4.6.2 DRUM 4-38
Re-installation 4-39- PICK-OFF PAWLS 4-40
Pick-off Pawl Position Adjustment 4-40 - CHARGE ROLLER AND CLEANING ROLLER 4-41
- DRUM CLEANING BLADE 4-42
Re-installation 4-42 - ID SENSOR 4-43
- PICK-OFF PAWLS 4-40
- DEVELOPMENT 4-44
- DEVELOPMENT FILTER 4-44
- DEVELOPMENT ROLLER 4-44
Cleaning Procedure 4-45 - DEVELOPER 4-46
- TD SENSOR 4-49
- TRANSFER 4-50
- TRANSFER BELT UNIT 4-50
- TRANSFER BELT 4-51
- TONER OVERFLOW SENSOR 4-53
- TRANSFER BELT CLEANING BLADE/TONER OVERFLOW SENSOR 4-53
Transfer Belt Cleaning Blade 4-53
Toner Overflow Sensor 4-54
- PAPER FEED 4-55
- PAPER FEED UNIT 4-55
Tray 1 and Tray 2 4-55 - PICK-UP, FEED AND SEPARATION ROLLERS 4-56
Tray 1 and Tray 2 4-56 - TRAY LIFT MOTOR 4-57
- RELAY, TRAY LIFT, PAPER END AND PAPER FEED SENSORS 4-58 Tray 1 and Tray 2 4-58
- REGISTRATION SENSOR 4-59
Reinstall the registration sensor 4-60
- PAPER FEED UNIT 4-55
- FUSING 4-61
- FUSING UNIT 4-61
- WEB ROLLER UNIT 4-62
- BRAKE PAD 4-62
- WEB HOLDER ROLLER AND WEB ROLLERS 4-63
Installing a new web holder roller 4-65
Installing new web rollers 4-65 - PRESSURE ROLLER CLEANING ROLLER 4-66
- THERMOSTATS 4-67
- THERMISTOR 4-68
- HOT ROLLER STRIPPERS 4-69
- FUSING LAMPS 4-70
- HOT ROLLER AND PRESSURE ROLLER 4-71
- PAPER EXIT 4-72
- PAPER EXIT UNIT 4-72
- FUSING EXIT, PAPER OVERFLOW, AND PAPER EXIT SENSORS 4-73
- JUNCTION JAM SENSOR 4-73
- PAPER EXIT MOTOR 4-74
- DUPLEX 4-75
- DUPLEX UNIT 4-75
- RIGHT DOOR COVER 4-77
- DUPLEX DOOR SENSOR 4-77
- DUPLEX ENTRANCE SENSOR 4-78
- DUPLEX EXIT SENSOR 4-79
- DUPLEX/BY-PASS MOTOR 4-81
- DUPLEX INVERTER MOTOR 4-82
- BY-PASS 4-84
- BY-PASS PAPER SIZE SENSOR/BY-PASS PAPER LENGTH SENSOR 4-84
When reinstalling the by-pass paper size sensor 4-86 - BY-PASS PAPER END SENSOR 4-87
- BY-PASS PICK-UP, FEED AND SEPARATION ROLLER, TORQUE LIMITER 4-87
- BY-PASS FEED CLUTCH 4-88
- BY-PASS PAPER SIZE SENSOR/BY-PASS PAPER LENGTH SENSOR 4-84
- DRIVE AREA 4-89
- PAPER FEED CLUTCH 4-89
Tray 1 and Tray 2 4-89 - DEVELOPMENT PADDLE MOTOR 4-90
- TRANSFER/DEVELOPMENT MOTOR 4-90
- DRUM MOTOR 4-91
- FUSING MOTOR 4-91
- WEB MOTOR 4-92
- PAPER FEED MOTOR 4-92
- TRANSFER BELT CONTACT MOTOR 4-93
- REGISTRATION MOTOR. 4-93
- TONER SUPPLY MOTOR 4-94
- PAPER FEED CLUTCH 4-89
- ELECTRICAL COMPONENTS 4-95
- CONTROLLER UNIT 4-95
- HDD UNIT 4-96
Before Replacing the HDD Unit 4-96
Replacement Procedure 4-96
After installing the new HDD unit 4-97 - CONTROLLER BOARD 4-98
Before Replacing the Controller Board in the Model without HDD 4-98
Replacement Procedure 4-98
When Installing the New Controller Board 4-100 - AFTER INSTALLING THE CONTROLLER BOARD 4-101
- MOTHER BOARD 4-101
4.15.7 IPU 4-104
4.15.8 IOB 4-105
When installing a new IOB 4-105
4.15.9 PSU 4-105- HIGH VOLTAGE POWER SUPPLY 4-106
- FUSING EXHAUST FAN 4-106
When installing the fusing exhaust fan 4-106 - CONTROLLER FAN 4-107
When installing the controller fan 4-107 - NVRAM ON THE BCU BOARD 4-108
Replacement procedure for the NVRAM on the BCU Board 4-108
- COPY ADJUSTMENTS: PRINTING/SCANNING 4-109
Registration: Platen Mode 4-114- OVERVIEW 4-109
- PRINTING 4-109
Registration - Leading Edge/Side-to-Side 4-109
Blank Margin 4-111
Main Scan Magnification 4-112
Parallelogram Image Adjustment 4-112
SM vii D129/D130 - SCANNING 4-114
4.16.4 ADF 4-116
Registration 4-116
4.16.5 TOUCH SCREEN CALIBRATION 4-117
- GENERAL CAUTIONS 4-1
- SERVICE TABLES 5-1
- SERVICE PROGRAM MODE 5-1
- SERVICE PROGRAM MODE OPERATION 5-1
Service Mode Lock/Unlock 5-1 - SERVICE PROGRAM MODE TABLES 5-2
Service Table Key 5-2
- SERVICE PROGRAM MODE OPERATION 5-1
- SERVICE PROGRAM MODE TABLES 5-3
- SP TABLES 5-3
- MAIN SP TABLES-1 5-4
- SP1-XXX: FEED 5-4
- MAIN SP TABLES-2 5-13
- SP2-XXX: DRUM 5-13
- MAIN SP TABLES-3 5-18
- SP3-XXX: PROCESS 5-18
- MAIN SP TABLES-4 5-19
- SP4-XXX: SCANNER 5-19
- MAIN SP TABLES-5 5-41
- SP5-XXX: MODE 5-41
- MAIN SP TABLES-6 5-108
- SP6-XXX: PERIPHERALS 5-108
- MAIN SP TABLES-7 5-117
- SP7-XXX: DATA LOG 5-117
- MAIN SP TABLES-8 5-132
- SP8-XXX: DATA LOG 2 5-132
- MAIN SP TABLES-9 5-183
- INPUT CHECK TABLE 5-183
Copier 5-183
Table 1: Paper Height Sensor 5-186
Table 2: Paper Size Switch 5-187
Table 3: Paper Size (By-pass Table) 5-188
APS Original Size Detection 5-189
3000/2000-Sheet (Booklet) Finisher (D636/D637) 5-190
D129/D130 viii SM
1000-Sheet Finisher (D588) 5-193 - OUTPUT CHECK TABLE 5-194
Copier 5-194
1000-Sheet Finisher (D588) 5-199
3000 /2000-Sheet (Booklet) Finisher (D636/D637) 5-200 - PRINTER SERVICE TABLES 5-202
SP1-XXX (Service Mode) 5-202 - SCANNER SERVICE TABLES 5-210
SP1-xxx (System and Others) 5-210
SP2-XXX (Scanning-image quality) 5-211
- INPUT CHECK TABLE 5-183
- UPDATING THE FIRMWARE 5-212
- BEFORE YOU BEGIN 5-212
- UPDATING FIRMWARE 5-213
Preparation 5-213
Updating Procedure 5-213
Error Messages 5-215
Firmware Update Error 5-215
Recovery after Power Loss 5-215 - HANDLING FIRMWARE UPDATE ERRORS 5-216
Error Message Table 5-216
- UPLOADING/DOWNLOADING NVRAM DATA 5-218
- UPLOADING NVRAM DATA (SP5-824) 5-218
- DOWNLOADING NVRAM DATA (SP5-825). 5-219
- SELF-DIAGNOSTIC MODE 5-221
- SELF-DIAGNOSTIC MODE AT POWER ON 5-221
- SELF-DIAGNOSTIC TEST FLOW 5-222
- DETAILED SELF-DIAGNOSTIC MODE 5-223
- EXECUTING DETAILED SELF-DIAGNOSIS 5-223
- USING THE DEBUG LOG 5-224
- OVERVIEW 5-224
- SWITCHING ON AND SETTING UP SAVE DEBUG LOG 5-224
4-Digit Entries for Keys 1 to 10 5-226
Key to Acronyms 5-227
Retrieving the Debug Log from the HDD 5-228
Recording Errors Manually 5-228
- SERVICE PROGRAM MODE 5-1
- TROUBLESHOOTING 6-1
- SERVICE CALL CONDITIONS 6-1
- SUMMARY 6-1
SM ix D129/D130 - SC CODE DESCRIPTIONS 6-2
SC Tables: SC1xx 6-3
SC Tables: SC2xx 6-6
SC Tables: SC3xx 6-8
SC Tables: SC4xx 6-11
SC Tables: SC5xx 6-12
SC Tables: SC6xx 6-21
SC Tables: SC7xx 6-30
SC Tables: SC8xx 6-42
SC Tables: SC9xx 6-65
- SUMMARY 6-1
- ELECTRICAL COMPONENT DEFECTS 6-71
- SENSORS 6-71
- SWITCHES 6-75
- BLOWN FUSE CONDITIONS 6-76
- FUSES 6-77
- SERVICE CALL CONDITIONS 6-1
D129/D130 x SM
Read This First
Safety Notices
Important Safety Notices
Prevention of Physical Injury
- Before disassembling or assembling parts of the copier and peripherals, make sure that the copier power cord is unplugged.
- The wall outlet should be near the copier and easily accessible.
- Note that some components of the copier and the paper tray unit are supplied with electrical voltage even if the main power switch is turned off.
- If any adjustment or operation check has to be made with exterior covers off or open while the main switch is turned on, keep hands away from electrified or mechanically driven components.
- If the Start key is pressed before the copier completes the warm-up period (the Start key starts blinking red and green alternatively), keep hands away from the mechanical and the electrical components as the copier starts making copies as soon as the warm-up period is completed.
- The inside and the metal parts of the fusing unit become extremely hot while the copier is operating. Be careful to avoid touching those components with your bare hands.
- To prevent a fire or explosion, keep the machine away from flammable liquids, gases, and aerosols.
- Toner and developer are non-toxic, but if you get either of them in your eyes by accident, it may cause temporary eye discomfort. Immediately wash eyes with plenty of water. If unsuccessful, get medical attention.
- This machine, which uses a high voltage power source, can generate ozone gas. High ozone density is harmful to human health. Therefore, the machine must be installed in a well-ventilated room.
- This machine and its peripherals must be serviced by a customer service representative who has completed the training course on those models.
- The NVRAM on the system control board has a lithium battery which can explode if replaced incorrectly. Replace the NVRAM only with an identical one. The manufacturer recommends replacing the entire NVRAM. Do not recharge or burn this battery. Used NVRAM must be handled in accordance with local regulations.
- Work carefully when removing paper jams or replacing toner bottles or cartridges to avoid spilling toner on clothing or the hands.
- If toner is inhaled, immediately gargle with large amounts of cold water and move to a well ventilated location. If there are signs of irritation or other problems, seek medical attention.
- If toner gets on the skin, wash immediately with soap and cold running water.
- If toner gets into the eyes, flush the eyes with cold running water or eye wash. If there are signs of irritation or other problems, seek medical attention.
- If toner is swallowed, drink a large amount of cold water to dilute the ingested toner. If there are signs of any problem, seek medical attention.
- If toner spills on clothing, wash the affected area immediately with soap and cold water. Never use hot water! Hot water can cause toner to set and permanently stain fabric.
- Always store toner and developer supplies such as toner and developer packages, cartridges, and bottles (including used toner and empty bottles and cartridges) out of the reach of children.
- Always store fresh toner supplies or empty bottles or cartridges in a cool, dry location that is not exposed to direct sunlight.
- Do not use the cleaner to suck spilled toner (including used toner). Sucked toner may cause firing or explosion due to electrical contact flickering inside the cleaner. However, it is possible to use the cleaner designed for dust explosion-proof purpose. If toner is spilled over the floor, sweep up spilled toner slowly and clean remainder with wet cloth.
Safety and Ecological Notes for Disposal- Do not incinerate toner bottles or used toner. Toner dust may ignite suddenly when exposed to an open flame.
- Dispose of used toner, the maintenance unit which includes developer or the organic photoconductor in accordance with local regulations. (These are non-toxic supplies.)
- Dispose of replaced parts in accordance with local regulations.
- When keeping used lithium batteries in order to dispose of them later, do not put more than 100 batteries per sealed box. Storing larger numbers or not sealing them apart may lead to chemical reactions and heat build-up.
Laser Safety
The Center for Devices and Radiological Health (CDRH) prohibits the repair of laser-based optical units in the field. The optical housing unit can only be repaired in a factory or at a location with the requisite equipment. The laser subsystem is replaceable in the field by a qualified Customer Engineer. The laser chassis is not repairable in the field. Customer engineers are therefore directed to return all chassis and laser subsystems to the factory or service depot when replacement of the optical subsystem is required.
- Use of controls, or adjustment, or performance of procedures other than those specified in this manual may result in hazardous radiation exposure.
- Turn off the main switch before attempting any of the procedures in the Laser Optics Housing Unit section. Laser beams can seriously damage your eyes.
CAUTION MARKING:
Conventions in this Manual
Symbols and Abbreviations
This manual uses several symbols and abbreviations. The meaning of those symbols and abbreviations are as follows:
See or Refer to
Clip ring
Screw
Connector
Clamp
E-ring SEF Short Edge Feed LEF Long Edge Feed
Cautions, Notes, etc.
The following headings provide special information:
- FAILURE TO OBEY WARNING INFORMATION COULD RESULT IN SERIOUS INJURY OR DEATH.
- Obey these guidelines to ensure safe operation and prevent minor injuries.
- This information provides tips and advice about how to best service the machine.
- Use of controls, or adjustment, or performance of procedures other than those specified in this manual may result in hazardous radiation exposure.
PRODUCT INFORMATION
RE V IS ION H IST ORY Page Date Added/ Updated/ New None
Product Information
PRODUCT INFORMATION
- SPECIFICATIONS
See "Appendices" for the following information:
- SPECIFICATIONS
- Do not use the cleaner to suck spilled toner (including used toner). Sucked toner may cause firing or explosion due to electrical contact flickering inside the cleaner. However, it is possible to use the cleaner designed for dust explosion-proof purpose. If toner is spilled over the floor, sweep up spilled toner slowly and clean remainder with wet cloth.
- General Specifications
- Optional Equipment
Machine Configuration
- MACHINE CONFIGURATION
- COPIER
Key: Symbol: U: Unique option, C: Option also used with other products
Item Callout Key Machine Code
CopierD129/D130 [1] - D129/D130 Platen Cover (See Note 1) [2] C D593 ARDF (See Note 1) [3] C D630 2000-sheet LCT [4] C D581 1200-sheet LCT [5] C D631 Two-Tray Paper Feed Unit [6] C D580 1-Bin Tray [7] U D632
Product Information
Machine Configuration
Item Callout Key Machine Code Bridge Unit [8] C D634 Internal Shift Tray [9] U D633 Side Tray [10] U D635 1000-sheet Finisher (See Note 2) [11] C D588 2000-Sheet Booklet Finisher (See Note 2)
[12]
C
D6373000-Sheet Finisher (See Note 2) [13] C D636
-Punch Unit (See Note 3)
-
CD570-00 (2/3-hole) NA
-Punch Unit (See Note 3)
-
CD570-01 (2/4-hole) EU
-Punch Unit (See Note 3)
-
CD570-02 (4-hole)
ScandinaviaKey Counter Bracket - C A674 HDD (for basic model only) - U D640 Copy Data Security Unit - C B829
FaxFax Option - U D629 G3 Interface Unit - U D629 SAF Memory - C G578 Handset - C D645 Fax Communication Unit - U D629
Printer/ ScannerPrinter/Scanner Unit - U D641 Printer Unit - U D641 Scanner Upgrade Unit - U D641 PostScript3 Unit - U D641
Item Callout Key Machine Code IPDS Unit - U D641 Gigabit Ethernet - C G874 IEEE 1284 - C B679 IEEE 802.11a/g, g - C D377 Bluetooth - C D566 Memory Unit 512 MB - C D594 File Format Converter - C D377 Browser Unit - U D640 VM Card - C D640 Netware - U D629
NOTE:- The ARDF and platen cover cannot be installed together.
- The finisher requires the bridge unit and two-tray paper feed unit or 2000-sheet LCT. The 1000-sheet finisher and 2000/3000-sheet (Booklet) finisher cannot be installed together.
- The punch unit requires the 2000/3000-sheet (Booklet) finisher.
Guidance for Those Who are Familiar with Predecessor Products
Product Information
- COPIER
- GUIDANCE FOR THOSE WHO ARE FAMILIAR WITH PREDECESSOR PRODUCTS
The D129/D130 series are successor models to the D091/D092 series. If you have experience with the predecessor products, the following information will be of help when you read this manual.
Different Points from Predecessor Products
D129/D130 D091/D092 Controller Type GW+ Controller GW Controller Operation Panel Tilt Operation Panel Type Includes USB/SD slot (not all functions can be used in Basic models) Stationary Operation Panel Type Scanner Lamp LED Xenon Safety Shut Down Function Available Not Available PDF Direct Standard (SP model only) Included in Printer/Scanner. Option App2Me Standard (SP model only) Included in Printer/Scanner, Printer SD Card.
Users who bought the VM card can download App2Me from the Web Site.Standard (SP model only) Included in VM SD Card. Data Overwrite Security Standard Option HDD Encryption Standard Option
- OVERVIEW
- COMPONENT LAYOUT
1 Exposure Glass 21 By-pass Feed Roller 2 2nd Mirror 22 By-pass Separation Roller 3 1st Mirror 23 Duplex/by-pass transport roller 4 Exposure Lamp 24 Upper Relay Belt 5 Original Length Sensors 25 Feed Roller 6 Scanner Motor 26 Separation Roller
Overview
7 Lens 27 Pick-up Roller 8 SBU 28 Bottom Plate 9 Junction Gate 2 29 Development Unit 10 Duplex Inverter Gate 30 Charge Roller 11 Duplex Entrance Sensor 31 F 12 Duplex Inverter Roller 32 Barrel Toroidal Lens (BTL) 13 Hot Roller 33 Polygonal Mirror Motor 14 Pressure Roller 34 Laser Unit 15 Transfer Belt Cleaning Blade 35 Toner Bottle Holder 16 Duplex Transport Roller 36 Junction Gate 1 17 Transfer Belt 37 Exit Roller 18 OPC Drum 38 Paper Exit Sensor 19 Registration Roller 39 3rd Mirror 20 By-pass Pick-up Roller 40 Scanner HP Sensor
- PAPER PATH
1 ARDF 2 Interchange Unit 3 Duplex Unit 4 By-pass Tray 5 Large Capacity Tray (LCT: 1200-sheet) 6 Paper Tray Unit 7 Two-Tray Finisher 8 Bridge Unit 9 1-Bin Tray
Product Information
- DRIVE LAYOUT
1 Scanner Motor 10 Paper Feed Clutch 1 2 Fusing Motor 11 Feed Motor 3 Web Motor 12 By-pass Paper Feed Clutch 4 Transfer/Development Motor 13 Registration Motor 5 Drum Motor 14 Duplex/By-pass Motor 6 Development Paddle Motor 15 Transfer Belt Contact Motor 7 Tray Lift Motor 1 16 Duplex Inverter Motor 8 Tray Lift Motor 2 17 Paper Exit Motor 9 Paper Feed Clutch 2
INSTALLATION
REVISION HISTORY Page Date Added/ Updated/ New 83 ~ 93 04/20/2012 Added Browser Unit Type I 94 ~ 102 04/23/2012 Added Fax Connection Unit Type A (D629-31)
- COMPONENT LAYOUT
- MACHINE CONFIGURATION
INSTALLATION
- INSTALLATION REQUIREMENTS
Installation
- Never turn off the main power switch when the power LED is lit or flashing. To avoid damaging the hard disk or memory, press the operation power switch to switch the power off, wait for the power LED to go off, and then switch the main power switch off.
- Install the machine in a safe place for keeping security.
- Make sure that the operation instructions are kept at a customer's hand.
- The main power LED lights or flashes while the platen cover or ARDF is open, while the main machine is communicating with a facsimile or the network server, or while the machine is accessing the hard disk or memory for reading or writing data.
- Rating voltage for peripherals: Make sure to plug the cables into the correct sockets.
- ENVIRONMENT
Temperature Range: 10°C to 32°C (50°F to 90°F) Humidity Range: 15% to 80% RH Ambient Illumination: Less than 1,500 lux (do not expose to direct sunlight.) Ventilation: Room air should turn at least 30 m3/hr/person Ambient Dust: Less than 0.10 mg/m3 (2.7 x 10/6 oz/yd3) - Avoid areas exposed to sudden temperature changes:
- Areas directly exposed to cool air from an air conditioner.
- Areas directly exposed to heat from a heater.
- Do not place the machine where it will be exposed to corrosive gases.
- Do not install the machine at any location over 2,000 m (6,500 ft.) above sea level.
- Place the main machine on a strong and level base. Inclination on any side should be no more than 5 mm (0.2").
- Do not place the machine where it may be subjected to strong vibrations.
- Avoid areas exposed to sudden temperature changes:
- MACHINE LEVEL
Front to back: Within 5 mm (0.2") of level Right to left: Within 5 mm (0.2") of level
- MINIMUM SPACE REQUIREMENTS
Installation
Place the main machine near the power source, providing clearance as shown:
- Never turn off the main power switch when the power LED is lit or flashing. To avoid damaging the hard disk or memory, press the operation power switch to switch the power off, wait for the power LED to go off, and then switch the main power switch off.
- INSTALLATION REQUIREMENTS
- Front [A]: Over 75 cm (29.6")
- Left : 10 cm (4")
[*]Rear [C]: 10 cm (4")
[*]Right [D]: 55 cm (21.7")
- The 75 cm (29.6") recommended for the space at the front is for pulling out the paper tray only. If the operator stands at the front of the main machine, more space is required.
- POWER REQUIREMENTS
- Make sure that the wall outlet is near the main machine and easily accessible. Make sure the plug is firmly inserted in the outlet.
- Avoid multi-wiring.
- Be sure to ground the machine.
- Input voltage level:
North America 120 V, 60 Hz: More than 12.5 A Europe/Asia 220 V to 240V, 50 Hz/60 Hz: more than 7 A - Permissible voltage fluctuation: 10% to 15%
- Never set anything on the power cord.
Installation Flow Chart
- Input voltage level:
- POWER REQUIREMENTS
- INSTALLATION FLOW CHART
The following flow chart shows how to install the optional units more efficiently.
Bridge Unit: Needed for the finishers.
Paper Tray Unit or LCT 2000-sheet: Needed for the LCT 1200-sheet and finishers.
Main Machine Installation
- MAIN MACHINE INSTALLATION
- ACCESSORY CHECK
Installation
Check the quantity and condition of the accessories in the box against the following list:
Description Q'ty
1Decal – Energy Save (-91, -61, -17, -57, -18, -58, -27, -67,
-29, -69, -19, -59, -28, -68)
1
2Rating plate (-17, -18, -19, -21, -27, -28, -29, -57, -58, -59,
-61, -67, -69, -68)
13 Decal – VERMONT (-91, -17, -57, -18, -58) 1 4 Model Name Decal (-91, -92, 17, -57) 1 5 Decal – WEEE (-27, -67) 1 6 Main SW Decal 1 7 Decal – Eco Label (-21, -61) 1 8 Decal – Rohs (-21, -61) 1 9 Decal – Rohs date(-21, -61) 1 10 Decal – Certificates (-21, -61) 2 11 Decal – LASERCLASS1 (-19, -59, -28, -68, -21, -61) 1 12 Decal – Impoter (-19, -59) 1 13 Decal – SDK (-57, -58, -67, -69, -59, -68, -61) 1 14 Decal – Caution - Copy 1 15 Emblem Cover 1 16 Emblem 1 17 Decal – Brand 1 18 Warranty (-21, -61) 1
Description Q'ty 19 Quick Reference Guide – Safety (-27, -67) 1
20Sheet – Communication management – Blank (-27, -67,
-19, -59)
1
21Decal – Paper Tray (-91, -17, -57, -18, -58, -27, -67, -29,
-69, -19, -59, -28, -68, -21, -61)
122 Decal – Caution – Original (-91, -17, -57, -18, -58) 1 23 Sheet – EMC – Traceability (-27, -67) 1 24 Sheet – Name – Tel (-21, -61) 1 25 Stamp (-91, -17, -57, -18, -58, -) 1 26 Exposure Glass Cleaning Cloth 1 27 Cloth Holder 1 28 Ferrite Core 1
29Sheet – Exposure Glass (-91, -17, -18, -19, -21, -27, -28,
-29, -57, -58, -59, -61, -67, -69, -68)
130 Power Supply Cord 1
31CD-ROM: Operation Instruction (-91, -92, -17, -18, -21, -27,
-28, -29, -57, -58, -67, -69, -68)
132 CD-ROM: Driver (-57, -58, -67, -69, -68) 1 33 CD-ROM: Operation Instruction/Driver (-19, -59, -21, -61) 1
34Operation Instruction – Read This First
(-91, -92, -17, -18, -19, -21, -27, -29, -57, -58, -59, -61, -67,
-69)
1
35Operation Instruction – User Guide
(-91, -92, -17, -18, -19, -21, -27, -29, -57, -58, -59, -61, -67,
-69)
136 Sheet – EULA (-57, -58, -67, -68, -69, -19, -59, -21, -61) 1 37 Sheet – Caution (-57, -58, -67, -68, -69, -68, -61) 1
Description Q'ty
38CD-ROM: Operation Instruction - App 2 Me (-57, -58, -67, -69, -59)
1
39Quick Reference Guide - App 2 Me (-57, -58, -69, -59)
140 Quick Reference Guide – Start Up (-27, -67) 1 41 Sheet – Notes – Manual – CD (-19, -59, -21, -61) 1
Installation
- INSTALLATION PROCEDURE
Preliminary Procedures
Put the machine on the paper feed unit or the LCT first if you will install an optional paper feed unit or the optional LCT at the same time. Then install the machine and other options.
- Keep the shipping retainers after you install the machine. You may need them in the future if you transport the machine to another location.
- ACCESSORY CHECK
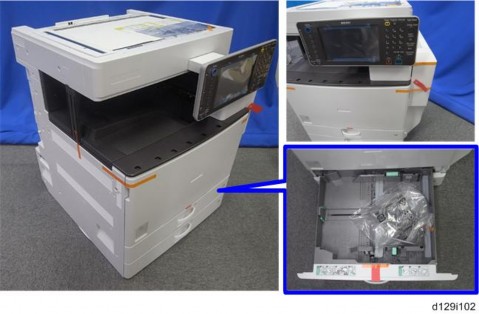
- Remove all the tapes and retainers on the machine.
- Remove all the tapes and retainers in trays 1 and 2, and then take out the power cord from tray 1 (if applicable).
Main Machine Installation
- Open the right door [A].
- Remove the two stoppers [A] from the fusing unit.
- Remove the scanner unit stay [A].
Main Machine Installation
Installation
- Open the front door [A], and then remove the jam location sheet .
[*]Keep the scanner unit stay [A] inside the front door .
[*]Reattach the jam location sheet.
[*]Close the front door.
Main Machine Installation
[*]Attach the correct brand decal to the machine [A].
[*]Attach the correct emblem and the cover to the front door of the machine, if the emblem is not attached.
- If you want to change the emblem that has been already attached, remove the panel with a small screwdriver, and then install the correct emblem.
[*]Pull out the feeler [A] for the output tray full detection mechanism.
PCDU (Photoconductor and Development Unit)
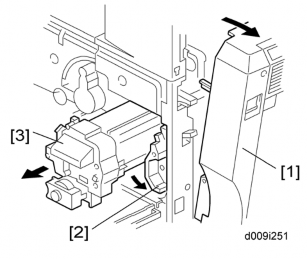
- Open the front door.
- Open the right door [1].
- Release the lock lever [2].
- Pull out the PCDU [3] and place it on a clean flat surface.
- Spread a large piece of paper on a flat surface.
Main Machine Installation
Installation
- Make sure the area is free of pins, paper clips, staples, etc. to avoid attraction to the magnetic development roller.
- Make sure the area is free of pins, paper clips, staples, etc. to avoid attraction to the magnetic development roller.
- Remove the opening cap [4], and then install it in the opening [5] of the PCDU.
- Open the PCDU [6]
- Remove the entrance seal plate [7]
- Remove the development roller unit [8], and set it on the paper.
Main Machine Installation
- Pour the developer [9] into the development unit.
- The developer lot number is embossed on the end of the developer package. Do not discard the package until you have recorded the lot number.
- Pour approximately 1/3 of the developer evenly along the length of the development unit.
- Rotate the drive gear [10] to work the developer into the unit.
- Repeat until all the developer is in the development unit.
- Continue to turn the drive gear until the developer is even with the top of the unit.
- The developer lot number is embossed on the end of the developer package. Do not discard the package until you have recorded the lot number.
- Put the opening cap [4] back in its original place.
- Reassemble the PCDU.
- Re-install the PCDU.
Installation
Toner Bottle
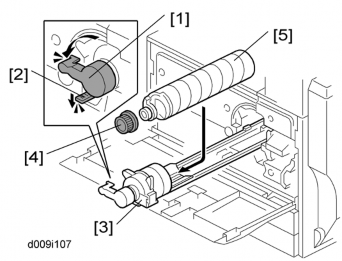
- Open the front door.
- Turn the toner bottle holder lever [1] counterclockwise, push down the lever [2], and then pull out the toner bottle holder [3].
- Hold the toner bottle [5] horizontally, and shake it 5 or 6 times.
- Unscrew the bottle cap [4] and set the bottle [5] in the holder.
- Push the toner bottle holder into the main machine until it locks in place.
- Turn the toner bottle holder lever [1] clockwise to lock it.
- Close the front door.
Paper Trays
- Open the 1st paper tray, and then press down on the right side of the lock switch to unlock the side fences.
- Press in on the sides of the fence release, and slide the side fences to the appropriate mark for the paper size.
- Pinch the sides of the end fence and move it to the appropriate mark for the paper size, then load the paper.
- Check the position of the stack.
- Confirm that there is no gap between the stack and the side fences. If you see a gap, adjust the position of the side fences.
- Press down the lock to lock the side fences.
- Repeat this procedure to load paper in the 2nd paper tray.
Initialize TD Sensor and Developer
- Connect the main machine to the power outlet, switch on the main machine, and wait for the fusing unit to warm up.
- Enter Copy SP Mode.
- Press SP Direct to highlight "SP Direct", enter 2801, and then press
- When the message prompts you to enter the lot number of the developer, enter the 7-digit lot number, press
- The lot number is printed on the end of the developer package. Recording the lot number could help troubleshoot problems later. If the lot number is unavailable, enter any seven-digit number.
- Press SP Direct to highlight "SP Direct" and enter 2805, press
- Press "Exit" twice to return to the copy window.
Set Paper Size for Paper Trays
- Press User Tools/Counter
- On the touch panel, press "System Settings".
- Press the "Tray Paper Settings" tab.
- Press the button for the tray to change.
- Change the setting and press the [OK] button.
- Repeat for each tray installed.
- Press Exit twice to return to the main display
- The 1st, 2nd, 3rd, and 4th paper trays are provided with the paper size switches. The detected paper size by the paper size switches has priority over the UP settings. However, if you change the "Auto Detect" with the UP setting, you can select the paper size.
- Check the copy quality and machine operation.
Electrical Total Counter
The electrical total counter no longer requires initialization. The new incrementing counter is set to "0" at the factory.
Main Machine Installation
Installation
Exposure Glass Cleaner
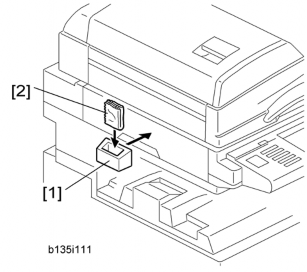
- Attach the exposure glass cleaner holder [1] to the left side of the machine.
- Place the exposure glass cleaner [2] inside the holder.
- The exposure glass cleaner is used to clean the ARDF exposure glass, the glass strip to the left of the large exposure glass.
Settings Relevant to the Service Contract
Change the necessary settings for the following SP modes if the customer has made a service contract.
Item | SP No. | Function | Default |
A3/11" x 17" double counting | SP5-104-001 (SSP) | Specifies whether the counter is doubled for A3/11" x 17" paper. When you have to change this setting, contact your supervisor. | "No": Single counting |
Service Tel. No. Setting | SP5-812-001 through 004 | 5812-002 programs the service station fax number. The number is printed on the counter list when the meter charge mode is selected. This lets the user fax the counter data to the service station. |
Data Overwrite Security
Do the following procedure if a customer wants to use this function.
- Do SP5-878-1(Option Setup - Data Overwrite Security) and touch [EXECUTE].
- Go out of the SP mode, turn off the operation switch, then turn off the main power switch.
- Turn the machine power on.
- Press [User Tools] and select System Setting > Administrator Tools > Auto Erase Memory Setting > On
- Exit from User Tools mode.
- Check the display and make sure that the overwrite erase icon [A] is displayed.
- Make a Sample Copy.
- Check the overwrite erase icon.
- The icon changes to [C] when job data is stored in the hard disk.
[*]The icon goes back to its usual shape after this function has completed a data overwrite operation to the hard disk.
[*]Do SP5990-005 (SP print mode - Diagnostic Report).
[*]Look at the report:
- Under "[ROM No./Firmware Version]" check the number and version number listed for "HDD Format Option".
- Under "[Loading Program]" check the option number and version number listed for "GW_zoffy".
- These two version numbers should be identical.
- The icon changes to [C] when job data is stored in the hard disk.
Main Machine Installation
HDD Encryption
Do the following procedure if a customer wants to use this function.
- Do SP5-878-2 (Option Setup - Encryption Option) and touch [EXECUTE]
- Go out of the SP mode, turn off the operation switch, then turn off the main power switch.
Installation
- Turn the machine power on.
- Push [User Tools] and select System Setting > Administrator Tools > Machine Data Encryption Setting.
- Press [Encrypt].
- Select the data to be carried over to the hard disk and not to be reset
To carry all of the data over to the hard disk, select [All data].To carry over only the machine setting data, select [File System Data Only]. To reset all of the data, select [Format All Data].
- Press the [Start] Key.
Main Machine Installation
App 2 Me Setting (SP model only)
SP models have VM and "App 2 Me" built in. Do the following procedure if a customer wants to use "App 2 Me".
- Press "User Tools" key on the operation panel.
- Touch the "Extended Feature Settings" button twice.
- Touch the "App 2 Me" line in the Startup Setting tab.
- Touch the "Extended Feature Info" tab on the LCD.
- Touch the "App 2 Me" line.
- Set the setting of "Auto Start" to "On".
- Touch the "Exit" button.
- Exit the "User Tools" settings.
- Push the "User/Tools" key.
- If an administrator setting is registered for the machine, steps 2 and 3 are required. Otherwise, skip to step 4.
- Push the "Login/Logout" key.
- Login with the administrator user name and password.
- Touch "Extended Feature Settings" twice on the LCD.
- Touch all the applications. Then, the status will be changed to "Stop".
- Turn off the machine. And then remove the VM Card.
- Prepare newer App 2 Me Provider zip file from Firmware Download Center. Unzip the zip file. (The folder name is "337051920".) And then copy the App 2 Me Provider folder in the specified path of VM card. The path is "SD_Card Drive¥ sdk¥dsdk¥dist¥337051920" as shown above.
Last edited: